Closed-loop Manufacturing: Steigern Digital Twins Innovation & Effizienz?
Die kurze Antwort lautet: Nicht lange! Denn in diesem Umfeld greifen die bisher herkömmlichen Produktionssysteme mit ihren nur lose verbundenen Konstruktions-, Produktions- und Betriebsprozessen oft zu kurz. Die Anforderungen neuer Technologien, strengere Vorschriften und kürzere Entwicklungszyklen übersteigen die Möglichkeiten traditionell linearer Ansätze.
Die Grenzen von isolierten Prozessen
Für Stefan Schmidt, einen erfahrenen Produktlinienmanager, wirkt sich jede Entscheidung auf Zeitpläne, Budgets und schlussendlich auch auf den Markterfolg aus. In seiner Rolle muss er Innovation gegen die unnachgiebigen Zwänge von Kosten, Qualität und Markteinführungsterminen miteinander abwägen.
Doch fragmentierte Arbeitsabläufe und isolierte Produktdaten stellen seine Teams trotz sorgfältiger Planung immer wieder vor enormen Herausforderungen:
- Verzögertes Feedback: In einer rein linearen oder „Open-Loop“-Umgebung kann es Monate dauern, bis Probleme, die während der Produktion oder der Inbetriebnahme entdeckt werden, an die entsprechenden R&D- und Konstruktionsteams weitergegeben werden.
- Hohes Risiko von Qualitätslücken: Wenn Produktionsdaten nicht kontinuierlich zurückgemeldet werden, können sich kleine Fehler in Materialien oder Prozessen zu Rückrufaktionen oder teuren Nacharbeiten ausweiten.
- Fragmentierte Datenlandschaft: Product Lifecycle Management (PLM), Manufacturing Execution System (MES) und Enterprise Resource Planning (ERP)-Systeme haben alle ihre Stärken, werden aber oft isoliert eingesetzt. Die beschränkt ganzheitliche Analysen oder funktionsübergreifende Erkenntnisse.
In Closed-Loop Manufacturing findet Stefan einen transformativen Verbündeten, der nicht nur seine Arbeit, sondern die Kultur des gesamten Unternehmen verändert hat.
Dank dieser strategischen Entscheidung seines Unternehmens profitiert Stefan nun von einem System, das über die standardmäßige Zustandsüberwachung und diskrete Engineering-Tools hinausgeht. Es bindet stattdessen den gesamten Produktlebenszyklus in eine kontinuierliche Rückkopplungsschleife ein und versetzt sein Team in die Lage, Herausforderungen mit noch nie dagewesener Flexibilität und Präzision anzugehen.
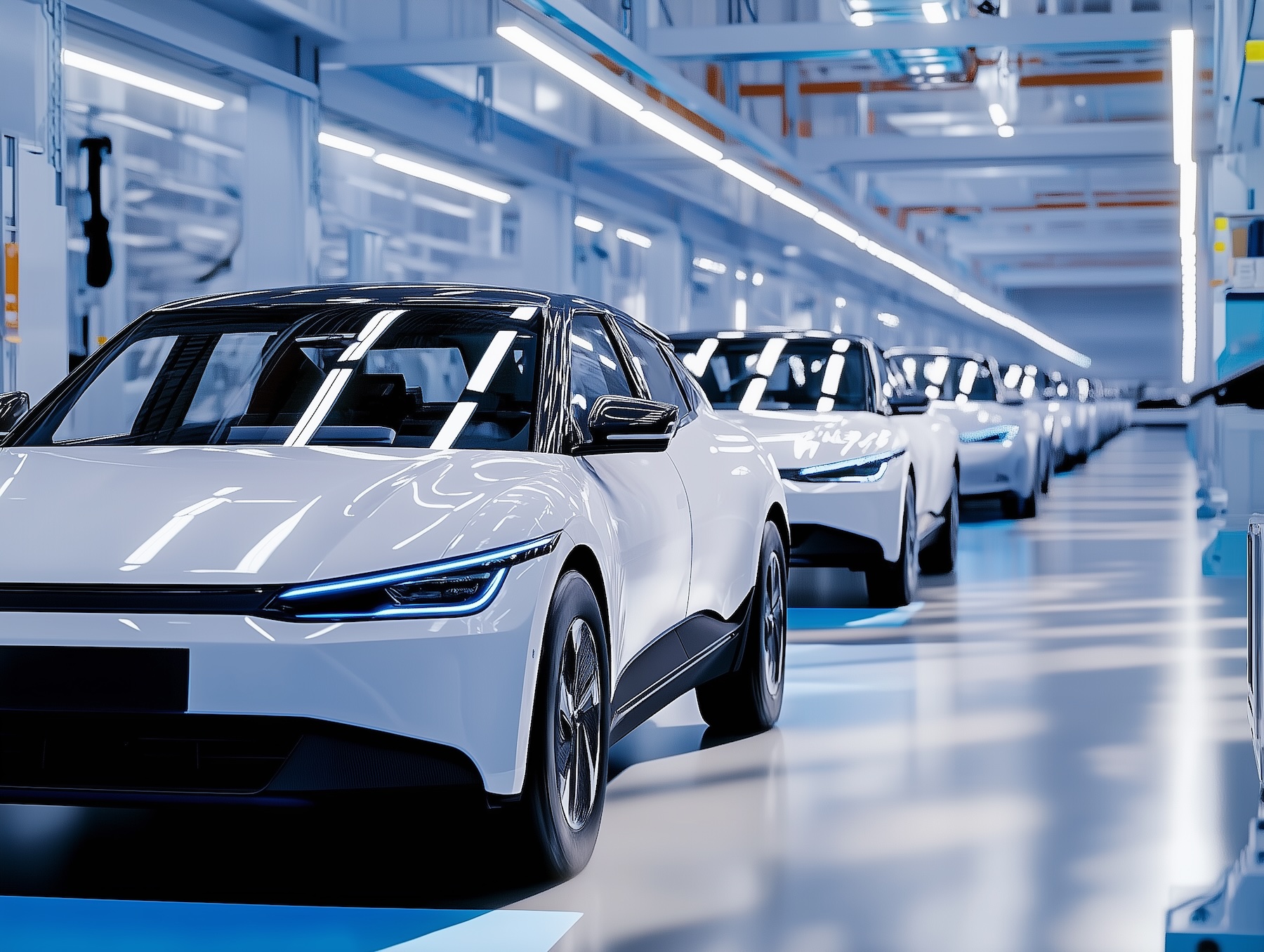
Was ist Closed-Loop Manufacturing (CLM)?
Closed-Loop Manufacturing schafft eine kontinuierliche Rückkopplungsschleife zwischen dem Design, der Produktion und der realen Leistung eines Produkts. Im Mittelpunkt dieses Ansatzes steht der digitale Zwilling, eine virtuelle Nachbildung physischer Produkte, Systeme oder Prozesse, die eine Brücke zwischen der digitalen und der physischen Welt schlägt.
Digitale Zwillinge ermöglichen es Teams, Abläufe in Echtzeit zu simulieren, zu optimieren und zu überwachen, wodurch Ineffizienzen drastisch reduziert und die Entscheidungsfindung verbessert werden. So konnte Stefans Team mit Hilfe von Digital Twins z.B. ein kritisches Problem bei der Kühlung von EV-Batterien lösen. Was früher Wochen dauerte, konnte dank der Erkenntnisse dieser Technologie nun in nur zwei Tagen gelöst werden.
Welche Rolle spielt der Digitale Zwilling im CLM?
Digitale Zwillinge sind dynamische, datengesteuerte Modelle, die die Echtzeitbedingungen und das Verhalten ihrer physischen Gegenstücke widerspiegeln. Durch die Nutzung von Daten aus IoT-Sensoren, Produktionssystemen, Produktdaten und der realen Nutzung ermöglichen sie den Herstellern Folgendes:
- Szenarien simulieren: Testen von Produkten unter verschiedenen Bedingungen - wie z. B. extremes Wetter oder Leistung in großer Höhe - ohne physische Tests.
- Prozesse optimieren: Verfeinerung von Produktionsabläufen durch Analyse von Echtzeitdaten auf Engpässe oder Ineffizienzen.
- Qualität steigern: Produktprobleme frühzeitig erkennen und eine schnelle Fehlerbehebung ermöglichen, insbesondere bei elektrischen, elektronischen und Softwarefehlern.
- Vorausschauende Wartung verbessern: Maschinen und Anlagen auf frühe Anzeichen von Verschleiß oder Ausfall überwachen und so ungeplante Ausfallzeiten vermeiden.
- Nachhaltigkeit fördern: Verschwendung identifizieren und die Ressourcennutzung verbessern, um Umweltziele zu erreichen.
Nach Stefans Erfahrung ermöglichte die Integration von Digital Twins in den Produktlebenszyklus seinem Team, Szenarien gemeinsam zu entwerfen, zu validieren und anzupassen. In diesem Zusammenhang ermöglichen sie z. B. detaillierte Simulationen, Leistungsoptimierungen, umfassendes Lebenszyklusmanagement oder Entscheidungsfindung in Echtzeit.
Durch die Bereitstellung einer zentralen Drehscheibe für Echtzeit-Einsichten befähigten Digital Twins sein Team, fundierte Entscheidungen zu treffen, die sowohl die Produktqualität als auch die Produktionseffizienz verbesserten.
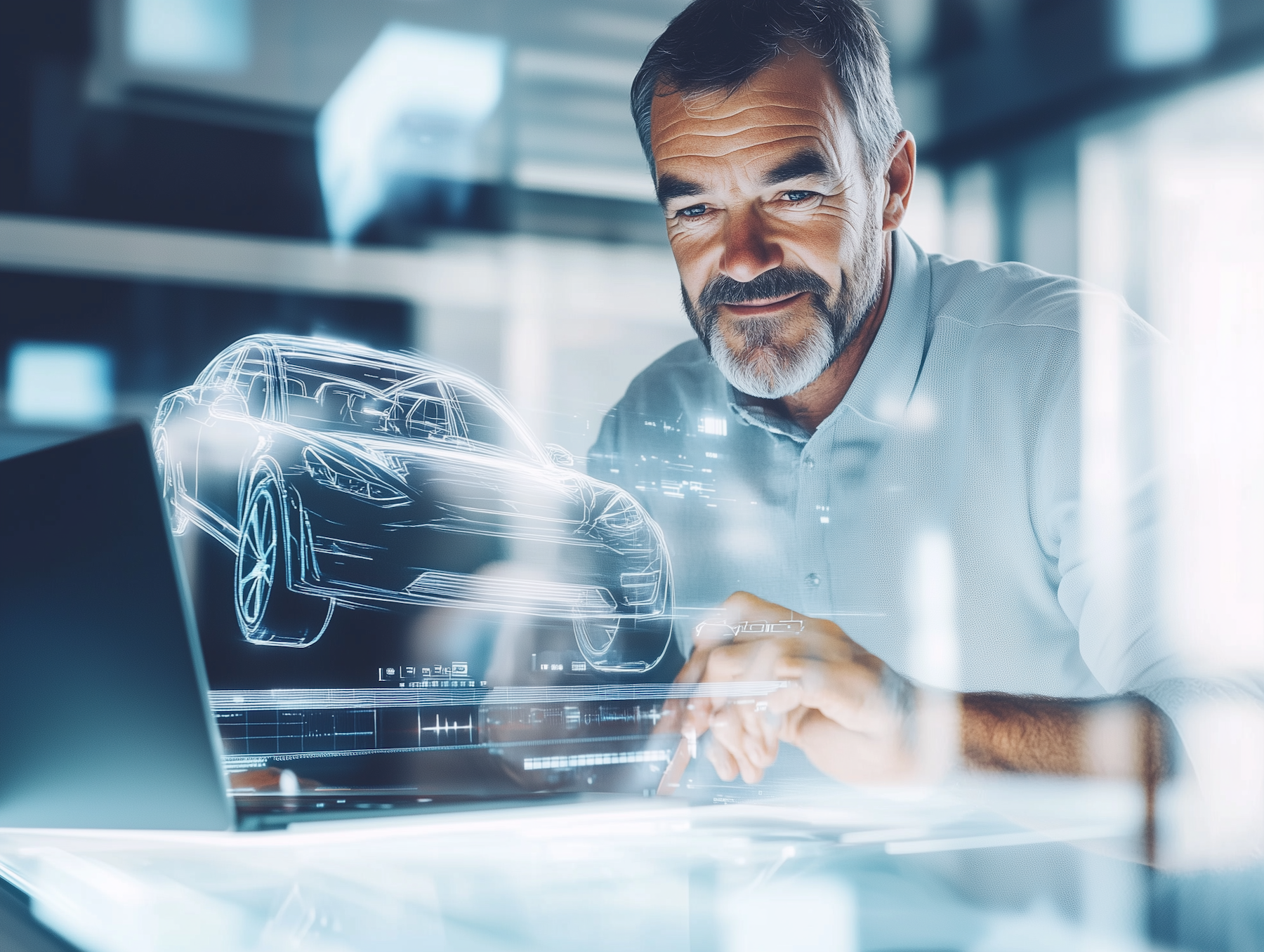
Ein Tag im Leben eines Produktionsleiters - jetzt wirklich „closed-loop“
Als Produktlinienmanager jongliert Stefan tagtäglich mit Kostendruck, Markteinführungsterminen und Qualitätsanforderungen. Vor der Einführung von CLM war Stefan von den langwierigen Kommunikationsschleifen zwischen Konstruktion, Prototypenbau und Produktion frustriert. Probleme, die beim Testen entdeckt wurden, dauerten Wochen, bis sie an die CAD-Teams weitergeleitet wurden, und die Maschinenbediener verfügten selten über Echtzeitdaten zu Designänderungen.
Der Morgen: Datengesteuerte Designverfeinerung mit unmittelbarer Wirkung
Stefan beginnt seinen Tag mit einem CLM-Dashboard, das Daten aus mehreren realen Quellen - IoT-Sensoren in der Produktion, Metriken der Lieferkette und Produkt- und Leistungsdaten aus verschiedenen Systemen in der Forschung und Entwicklung - zusammenfasst.
Ein sprunghafter Anstieg der Garantieansprüche für eine bestimmte EV-Batteriekühlungslinie wird sofort angezeigt. Anstatt auf eine geplante Projektüberprüfung zu warten, sehen Konstrukteure die genauen Bedingungen, die zu Kühlmittellecks führen, und können CAD-Modelle innerhalb von Stunden anpassen.
Nachmittags: Integrierte Produktionsanpassungen mit Echtzeit-Reaktion
Sobald die überarbeitete Konstruktion genehmigt ist, überträgt CLM automatisch neue Montageanweisungen - die mit Hilfe von Präzedenzgraphen sofort abgeleitet wurden - an das Manufacturing Execution System (MES) und stellt so sicher, dass Roboter-Montagestationen und Vorarbeiter aktuelle Schweißparameter erhalten.
Wenn das System eine potenzielle Fehlausrichtung in einer Schweißvorrichtung erkennt, sendet es eine Warnung zur sofortigen Kalibrierung. Die Produktion kann mit minimaler Ausfallzeit fortgesetzt werden.
Abend: Vollständiger Kreislauf der kontinuierlichen Verbesserung
Das System protokolliert alle Produktionsanomalien in der PLM-Umgebung und lässt die Erkenntnisse in die Konstruktionsrichtlinien einfließen. Dies löst auch Aktualisierungen des Simulationsmodells (Digitaler Zwilling) aus, das für künftige Designvalidierungen verwendet wird.
Am Ende des Tages verfügen die Konstruktionsteams über genauere Daten, um Produktänderungen zu planen, und der Kreislauf setzt sich nahtlos fort.
Stefans größte Erleichterung? Kein Rätselraten und keine blinden Annahmen mehr. Jede Design- oder Prozessverbesserung basiert auf echten, validierten Daten.
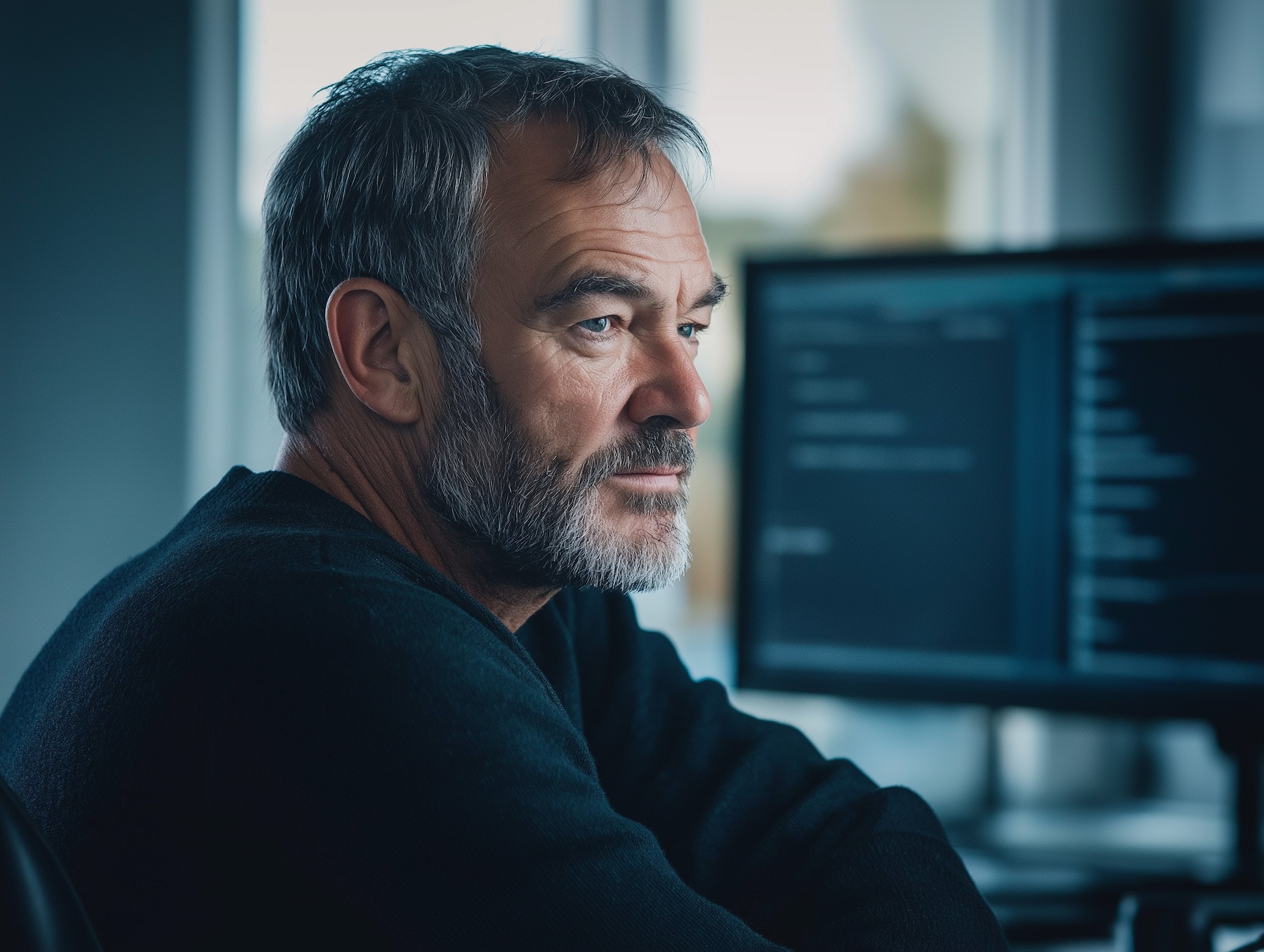
CLM vs. Vorausschauende Wartung (Predictive Maintenance)
Closed-Loop-Manufacturing einfach als eine weitere Ebene der vorausschauenden Wartung zu betrachten, liegt nahe, dochr CLM ist umfassender als das. Die zustandsorientierte oder vorausschauende Wartung konzentriert sich in der Regel auf die Überwachung des Anlagenzustands, um Ausfälle zu vermeiden (z. B. Vibrationen, Temperaturen).
Closed-Loop-Manufacturing hingegen geht noch einen Schritt weiter: Sie lässt alle betrieblichen Erkenntnisse in die Konstruktion, Forschung und Entwicklung sowie die Produktionsplanung einfließen. Produktdesigns und Prozessparameter werden auf der Grundlage realer Daten ständig feinabgestimmt, was iterative Verbesserungen während des gesamten Lebenszyklus ermöglicht.
Ein Zustandsüberwachungssystem könnte beispielsweise eine Warnung senden, dass ein Schweißroboterarm kurz vor dem Ausfall steht. Im CLM-System löst diese Warnung jedoch nicht nur Wartungsarbeiten aus, sondern informiert auch die Konstrukteure, damit sie die Schweißnahtgeometrie oder die Materialien für künftige Modelle optimieren und gleichzeitig die Parameter für die Produktionsausführung aktualisieren können.
CLM vs. PLM, MES, APQP und Digital Thread
Fachleute fragen oft: „Ist CLM nur bloß ein PLM oder MES mit einem neuen Namen?“ Die kurze Antwort lautet: Nein! Es baut vielmehr auf diesen Systemen auf, anstatt sie zu ersetzen.
- PLM (Produktlebenszyklus-Management): Verwaltet Produktdaten vom Konzept bis zur Entsorgung und konzentriert sich dabei auf Dokumentation, Revisionskontrolle und Zusammenarbeit. CLM nutzt PLM-Daten, stellt aber sicher, dass reale Leistungskennzahlen die Produktdefinitionen und Konstruktionsregeln kontinuierlich aktualisieren.
- MES (Manufacturing Execution System): Überwacht die Abläufe in der Produktion, z. B. Planung, Disposition und Ressourcenauslastung. CLM nutzt MES-Daten (z. B. Zykluszeiten, Ausschussraten), um Konstruktionsparameter zu verfeinern, während gleichzeitig Konstruktionsänderungen in MES-Anweisungen zurückgeführt werden.
- APQP (Advanced Product Quality Planning): Eine strukturierte Methode (vor allem in der Automobilindustrie) zur Sicherstellung der Produktqualität vom frühen Entwurf bis zur Produktion. CLM bringt Echtzeit-Feedback aus der Praxis in die APQP-Phasen ein, um Qualitätsprobleme proaktiv anzugehen.
- Digital Thread: Bezieht sich auf den nahtlosen Datenfluss während des gesamten Lebenszyklus. CLM ist eine Anwendung des Digital-Thread-Konzepts, die speziell auf ein Closed-Loop-Feedback zur kontinuierlichen Produkt- und Prozessoptimierung abzielt.
Kurz gesagt, CLM vereinheitlicht und orchestriert den Datenfluss zwischen all diesen Systemen und stellt sicher, dass sie als Teil eines kontinuierlichen, verbesserungsgetriebenen Kreislaufs funktionieren.
Was sind die vier Phasen des Closed-Loop-Manufacturing?
CLM umfasst vier Schlüsselphasen, die jeweils auf der vorhergehenden aufbauen, um eine kontinuierliche Verbesserung zu gewährleisten:
1. Produktdatenintegration und Rückverfolgbarkeit
Sorgt für einen nahtlosen Abgleich zwischen R&D und Produktion und reduziert so Fehler und kostspielige Nacharbeit. Stefans Team nutzte beispielsweise einen digitalen Zwilling, um einen Konstruktionsfehler in einem EV-Batteriekühlsystem schnell zu erkennen und zu korrigieren, wodurch die Lösungszeit auf nur wenige Tage verkürzt wurde.
2. Intelligente Produktion und Anpassungen in Echtzeit
IoT-fähige Systeme ermöglichen Echtzeitüberwachung und -anpassungen und verhindern so Verzögerungen. Ein Kalibrierungsfehler in einer Roboterschweißstation während der Vorproduktion wurde vom Digitalen Zwilling erkannt und in Echtzeit korrigiert, wodurch sowohl der Zeitplan als auch die Qualität eingehalten werden konnten.
3. Produkt- und Leistungsüberwachung und vorausschauende Wartung
Produkt- und Leistungsdaten aus der realen Welt fließen in die Digitalen Zwillinge ein und ermöglichen es den Teams, Probleme präventiv anzugehen. Stefans Team nutzte Digital Twins zum Beispiel zur Überwachung von Anomalien der Achsentemperatur bei Prototypen und konnte so Probleme lösen, bevor die Produktion begann.
4. Feedback-Schleifen treiben die Innovation voran
Daten aus dem realen Produktgebrauch fließen in die Konstruktion und Produktion ein, um kontinuierliche Verbesserungen zu ermöglichen. Stefans Team identifizierte beispielsweise Verschleißmuster in Aufhängungskomponenten und verfeinerte die Konstruktion, um Garantieansprüche zu reduzieren und die Haltbarkeit zu verbessern.
CLM implementieren: Deep Dive in Datenintegration, Sicherheit und Standards
Die effektive Implementierung von CLM erfordert mehr als nur die Verknüpfung von Sensoren und Produktdaten mit der Cloud.
Zu den wichtigsten Überlegungen gehören:
1. Datenqualität und Governance
Stellen Sie sicher, dass die Daten genau, standardisiert und nachvollziehbar sind. Eine schlechte Datenqualität kann zu Fehlalarmen oder verpassten Warnungen führen.
Setzen Sie robuste Governance-Richtlinien ein, um zu entscheiden, wie Daten erfasst, bereinigt, gespeichert und abgerufen werden.
2. Systemintegration
CLM interagiert in der Regel mit PLM-, MES- und ERP-Systemen sowie mit Lieferantenportalen, digitalen Zwillingen und Analyseplattformen.
Wählen Sie Integrationsansätze (APIs, Middleware oder direkte Datenbankverbindungen), die die manuelle Datenübertragung minimieren und das Risiko verringern.
Die Knowledge-Graph-Technologie erweist sich als Schlüssel zur Erstellung domänenspezifischer semantischer Modelle, die die Daten kontextualisieren und verwertbare Informationen im spezifischen Kontext der Benutzer ableiten.
Sie bilden auch die Grundlage für den sinnvollen Einsatz von KI-Modellen und Agenten.
3. Sicherheit und IP-Schutz
Der Datenaustausch in Echtzeit wirft Sicherheitsbedenken auf. Verschlüsselung, rollenbasierter Zugriff und sichere Datenpipelines sind von entscheidender Bedeutung - insbesondere in der Automobil- und Luftfahrtindustrie, wo geistiges Eigentum sehr sensibel sein kann.
Die Einhaltung branchenspezifischer Standards (z. B. TISAX in der Automobilindustrie, DO-326A / ED-202A in der Luft- und Raumfahrt) kann erforderlich sein.
4. Anpassung an Normen (IATF 16949, EN 9100, etc.)
CLM unterstützt die Rückverfolgbarkeitsanforderungen dieser Normen, indem es sicherstellt, dass der digitale Zwilling jedes Produkts automatisch aktualisiert wird, von der Konstruktion bis zu den Servicedaten im Feld.
Die automatische Dokumentationserstellung kann dazu beitragen, Audits und Qualitätskontrollpunkte schneller zu erfüllen, als dies mit manuellen Berichten je möglich wäre.
5. Organisationskultur und Prozesse
Die Implementierung von CLM erfordert häufig Änderungen der Teamrollen und der Arbeitsabläufe für die Zusammenarbeit. Die funktionsübergreifende Zusammenarbeit ist der Schlüssel, um sicherzustellen, dass Design-, Produktions-, Qualitäts- und Serviceteams eine gemeinsame „Datensprache“ sprechen.
Erfolge quantifizieren: Harte Fakten und KPIs von CLM
Die Einführung von Closed-Loop-Manufacturing (CLM) eröffnet eine Vielzahl von Vorteilen mit sich, die die Arbeitsweise der Hersteller verändern. Auch wenn die Ausgangssituation in jedem Unternehmen anders ist, gibt es doch einige allgemeine Kennzahlen, die sich durch CLM verbessern:
- Verkürzung der Markteinführungszeit: Um bis zu 20-40%, dank einer beschleunigten Designvalidierung und weniger Änderungen in der Spätphase.
- Qualitätsverbesserungen: 30-50% weniger Ausschuss oder Nacharbeit durch frühere Erkennung von Konstruktions- oder Produktionsfehlern.
- Vorausschauende Wartung ROI: Durch proaktive Planung und Konstruktionsaktualisierungen zur Behebung wiederkehrender Fehler werden die Ausfallzeiten von Anlagen oft um 25-50% reduziert.
- Reduzierung von Gewährleistungsansprüchen: Potenzieller Rückgang um 10-30% durch Echtzeit-Feedback aus dem Feld, das zu gezielten Konstruktionsverbesserungen führt.
Offener Kreislauf vs. geschlossener Kreislauf: Vergleich auf einen Blick
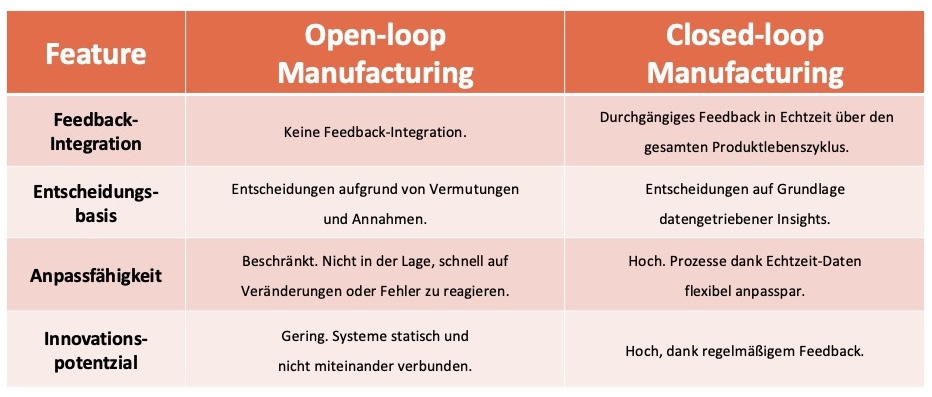
Mehr als die Gegenwart: Künftige Trends im CLM
Die Closed-Loop-Manufacturing entwickelt sich mehr und mehr zu selbstanpassenden Systemen, bei denen KI-Algorithmen sowohl die Design- als auch die Produktionsparameter kontinuierlich in Echtzeit verfeinern. Da immer mehr Fabriken 5G-Netzwerke und Edge Computing einsetzen, wird die Latenzzeit zwischen dem Erkennen eines Problems und der Durchführung einer Korrekturmaßnahme weiter sinken.
Dies ebnet den Weg für adaptive Produktionslinien, bei denen sich die Maschinen auf der Grundlage kleinerer Designänderungen oder Nachfrageverschiebungen neu konfigurieren. Außerdem können maschinelle Lernmodelle Probleme erkennen und vorhersagen sowie neue Designmöglichkeiten identifizieren. Diese Modelle ermöglichen eine lückenlose Rückverfolgung von Produkten, was die Transparenz erhöht und Echtzeitbewertungen des CO2-Fußabdrucks, des Materialverbrauchs und der Wiederverwertbarkeit eines Produkts ermöglicht.
Fazit: Die Zukunft der Produktion liegt im closed-loop
Für Hersteller in der Automobil- und Luft- und Raumfahrtindustrie ist CLM eine greifbare, datengesteuerte Strategie, die Sensorfeedback, Produktionsmetriken und reale Leistung in eine einzige kontinuierliche Feedbackschleife integriert. Durch die Schließung der Lücke zwischen Technik und Betrieb können sich Unternehmen schnell an Herausforderungen anpassen, strenge Qualitätsstandards einhalten und unermüdliche Innovationen vorantreiben.
In der Welt von Stefan Schmidt sind die Tage des Wartens auf sporadisches Feedback und isolierte Updates vorbei.
Jetzt fließen Echtzeitdaten nahtlos zwischen Konstruktion und Produktion, und jede Verbesserung in der Praxis treibt die nächste Welle der Produktinnovation voran. Das ist die Stärke der Closed-Loop-Manufacturing - und sie prägt die Zukunft der Entwicklung, Produktion und Optimierung von Produkten in den anspruchsvollsten Branchen der Welt.
Transformieren Sie Ihre Produktion mit SPREAD
Wir von SPREAD erwecken diese Vision zum Leben. Unsere Agentic Engineering Intelligence-Lösungen kombinieren fortschrittliche Analysen, Echtzeit-Datenintegration und branchenspezifisches Fachwissen, um messbare Ergebnisse zu erzielen. Lassen Sie uns Ihnen helfen, in dieser wettbewerbsintensiven Landschaft die Nase vorn zu haben. Setzen Sie sich noch heute mit uns in Verbindung, um Ihre Produktionsprozesse in einen zukunftssicheren Vorteil zu verwandeln.
Entdecken Sie, wie SPREAD Ihre Produktionsprozesse transformieren kann mit:
- Maßgeschneiderte digitale Zwillingslösungen: Entwickelt, um Ihre spezifischen Branchenanforderungen zu erfüllen.
- Erweiterte Analytik und KI-Integration: Nutzung der neuesten Erkenntnisse des maschinellen Lernens für fundierte Entscheidungen.
- Nahtlose Systemintegration: Sicherstellen, dass alle Phasen Ihres Produktionslebenszyklus reibungslos zusammenarbeiten.
Erfahren Sie mehr darüber, wie unsere innovativen Lösungen Ihre Produktionsumgebung verbessern, die Effizienz steigern und Ihr Unternehmen an der Spitze der Produktionsexzellenz halten können.