How Rheinmetall Air Defence improved change impact analysis - with a Defense Digital Twin
Driving sustainable long-term growth as global demand surges
The defense market is experiencing significant growth in sales and attention as international conflicts become more unpredictable. This surge in demand for defense capabilities has resulted in full order books for defense companies such as Rheinmetall AG, promising robust growth in the sector.
As a result, in the first half of 2024 alone, Rheinmetall AG’s Group sales climbed noticeably by more than 30%. At Division Electronic Solutions (e.g. air defense and digitalization technologies) order intake surged by more than 400%.
„In the second quarter of 2024 alone, our sales increased around 50 percent and our result more than doubled. […] We have never seen such growth. We also expect annual sales growth of around two billion euros in the coming years.” – Armin Pappberger, CEO Rheinmetall AG
As the demand of protection of critical infrastructure has surged, the Oerlikon Skyranger® 30 ground-based air defense (GBAD) system, built by Rheinmetall Air Defence (RAD) in Zurich, has been one of the drivers for this growth.
Recognizing the need to become more efficient to generate revenue from the surge in orders, RAD is looking to scale-up production of the Skyranger significantly. The company knows that a comprehensive approach is essential and sets out to enhance its productivity and efficiency through technological enablement and digital connectivity across all domains.
Mastering complexity
Hitherto mainly mechanical systems are becoming increasingly digital, more connected, containing more electronics and software. This rise of electrical/electronic (E/E) and software content brings more complexity, as market demands for even more advanced functions.
For example, the automotive industry today stands at the intersection of rapid technological evolution and intense regulatory evaluation, driven by the integration of advanced features like sensors, autonomous driving capabilities, and driver-assistance systems. Each of these features introduces new dependencies, creating a highly complex network of interconnected software and hardware components within vehicles.
For instance, a sensor that supports adaptive cruise control must seamlessly interface with both safety-critical braking systems and non-critical functions like infotainment. This interconnectedness amplifies the challenge of ensuring that each feature functions reliably and safely within the larger system, especially as vehicles increasingly rely on software updates and real-time data exchange to remain operationally compliant and efficient.
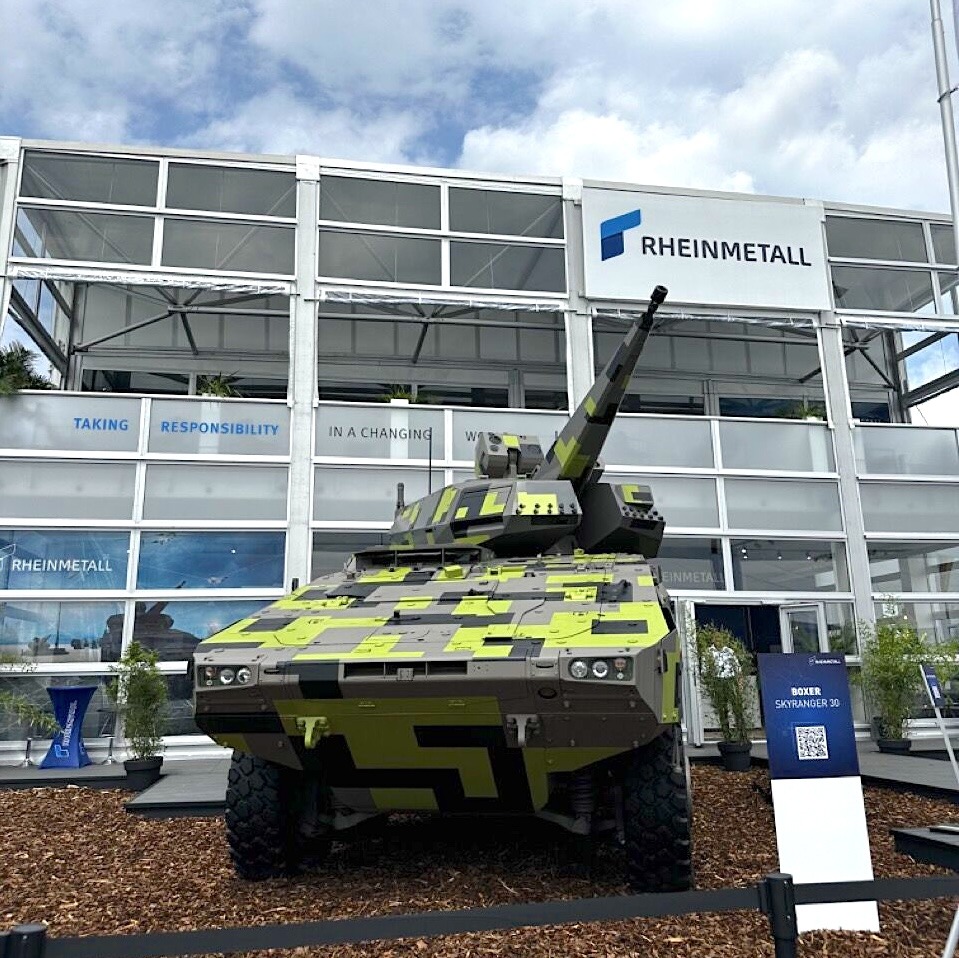
Mastering complexity in defense
At the same time, regulatory demands on automakers have become more stringent and multifaceted, requiring manufacturers to continuously meet safety standards, emissions regulations, and cybersecurity mandates. Every new software-defined feature in a vehicle has specific regulatory requirements that must be meticulously documented, tested, and validated across the lifecycle.
Compliance now extends beyond traditional physical inspections, moving into the realm of digital oversight, where software updates, data integrity, and real-time monitoring must meet regulatory approval. This environment creates substantial pressure on engineering teams to ensure that every part of the vehicle adheres to international standards, as even minor oversights can lead to costly recalls, delays, or legal repercussions. Consequently, automakers are tasked with not only achieving rapid innovation but also navigating a highly complex regulatory landscape.
The same applies to the defense systems where most sophisticated sensors and effectors are seamlessly coordinated and synchronized to achieve maximum effect in the most demanding environment. In case of Skyranger this means the integration of an Active Electronically Scanned Array (AESA) radar, high resolution optical tracking systems into a highly mobile turret, housing the high-powered air defense gun, all being controlled by the operator in the carrier vehicle.
This is why Rheinmetall Air Defence made an in-depth study to understand the benefits accompanying the physical product with a digital counterpart, the 3D digital twin.
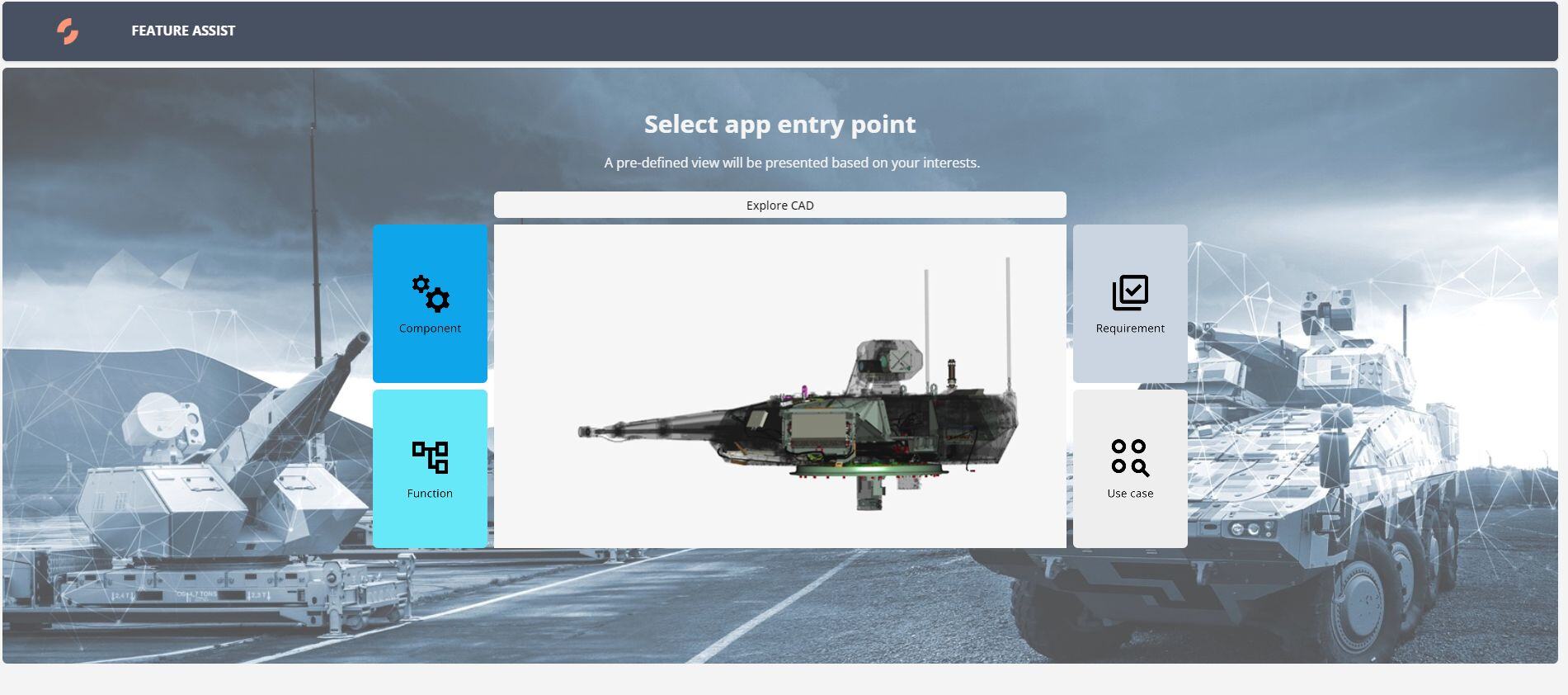
Benefits of the digital twin
A digital twin framework offers a revolutionary approach, enabling defense companies to create accurate virtual representations of how these systems work and communicate – like a human brain and nervous system, the Electronic Control Units (ECU) in the E/E architecture send signals throughout the entire system to drive actions (i.e. functions). Capturing a virtual representation of these communication flows and linkages facilitates up-to-date monitoring, predictive analysis, and seamless integration across various subsystems, improving reliability and efficiency across all engineering domains.
Gain a transparent view on product maturity
By connecting product data from multiple sources, engineers gain valuable insights into both product maturity and overall operational efficiency. This allows the engineering team to monitor the development, maturity and performance of critical components, helping them manage dependencies and identify potential issues before they escalate. Early detection of issues eliminates the need for redundant testing cycles, reducing unnecessary costs and maintaining quality standards.
With improved visibility into product maturity, teams can even predict delivery dates and address issues before they impact timelines. This enables managers to make informed decisions and provide reliable forecasts to stakeholders.
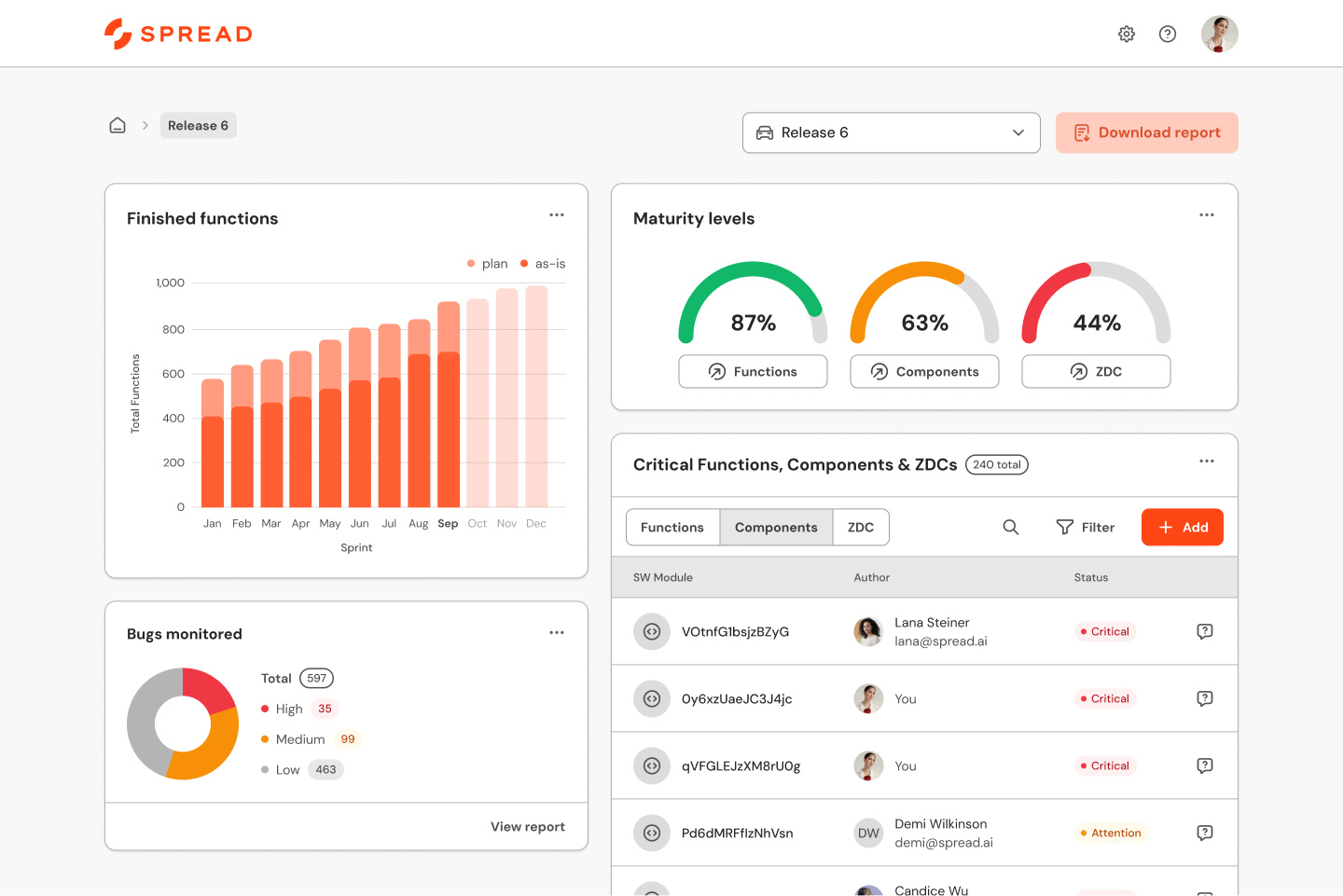
Improve cross-team collaboration
Due to the increase in interdependencies, the need for tighter collaboration across domains grows. The digital twin enables cross-functional teams at RAD to work on different modules in a coordinated manner.
While the mechanical engineers work with the 3D CAD data, the systems engineers can see all the requirements associated with a function or component - E/E architects can visualize electrical systems and dependencies, while wiring harness experts can design and verify connections in real-time. This means that engineers are working with real-life data. As data is updated, everyone has access to it. This collaborative approach minimizes errors and accelerates the development process.
Streamline knowledge management & upskilling
By capturing and centralizing complex product data, the digital twin provides a comprehensive and easily accessible knowledge base. This allows engineers and defense personnel to quickly familiarize themselves with system configurations, subsystems, and interdependencies. In the face of a growing shortage of skilled workers, this centralized knowledge becomes even more critical, as it enables less experienced personnel to get up to speed quickly and ensures that vital system information is readily available, reducing the reliance on specialized expertise.
For upskilling, the digital twin serves as a practical hands-on training tool, allowing new team members to interact with real-time system data and understand complex configurations through simulations. This drastically reduces onboarding time and ensures the team is equipped with accurate, up-to-date knowledge to handle evolving defense technologies effectively.
Speed up error management
The Skyranger digital twin allows engineers to minimize probability of failure and potentially prevent errors before they occur by providing a highly detailed representation of the system's components and functionalities. This includes performing Failure Mode and Effects Analysis (FMEA) and Fault Tree Analysis (FTA) within the digital environment allowing teams to proactively detect weaknesses and implement mitigation strategies.
Engineers may quickly pinpoint the root cause, assess the impact on interconnected components, and implement solutions more efficiently – all of which reduces system downtime while improving overall operational readiness in mission-critical environments.
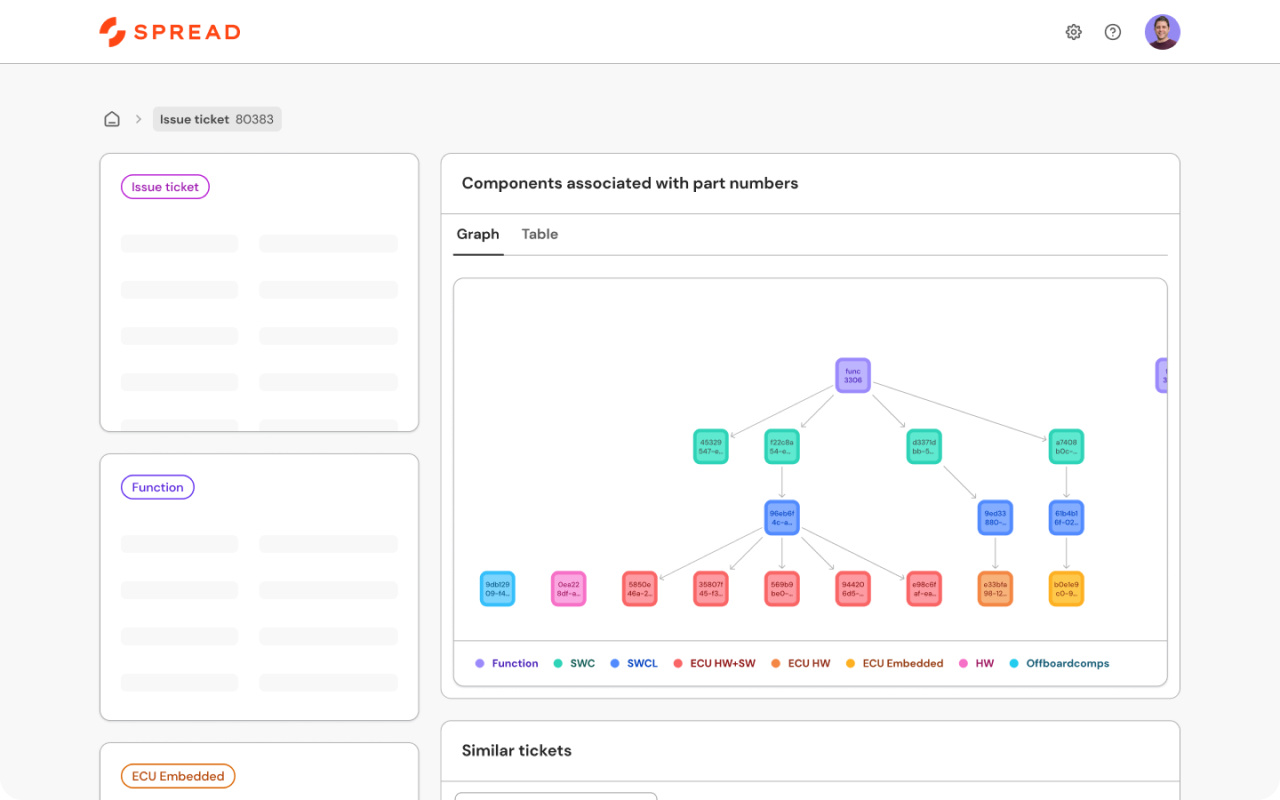
Scale production
The 3D digital twin helps scale operations by providing real-time insights in manufacturing. It helps streamlining workflows, resulting in faster, more scalable, error-free, and repeatable production processes.
Moreover, by extracting precedence graphs from 3D CAD models and BOM/parts list data, manual input can be reduced, ensuring accurate and efficient assembly steps. The algorithm doesn't just generate an arbitrary sequence - it geometrically calculates logical dependencies based on the spatial relationships and constraints present in the 3D model.
This approach enables spatial analysis, as well as constraint detection and dynamic adjustments. Users can validate and adjust the result in a web-based 3D model, allowing teams to seamlessly manage both parallel and sequential assembly steps.
Enable predictive/preventive maintenance
The 3D digital twin technology also enables predictive and preventive maintenance capabilities. Exploiting usage and lead-time data from the physical twin allows customers to manage their spare parts, ensuring mission readiness and resilience. the effect of delivery times is limited for the concerning system. As a result, predictive maintenance enabled by the 3D digital twin helps to minimize downtime, streamline repairs, and keep systems up and running for longer periods without unexpected interruptions.
Improve change impact analysis
As the Skyranger evolves to meet new threats, the digital twin ensures that updates are seamlessly incorporated into the system’s architecture.
This capability is particularly valuable in R&D, where design and technology modifications can be assessed virtually. Engineers can analyze changes in component layouts, materials, and configurations, including checks on, for example, wiring harness standards and requirements, voltage drop calculations, or sub-component specifications. This ensures that any adjustments are optimized before moving to production.
The Skyranger system has the flexibility to be deployed from a wide range of vehicles. As new variants are introduced, the digital twin system can automatically verify that each variant adheres to relevant standards and specifications. This approach ensures that each variant is developed and tested with minimal risk, saving time and ensuring compliance across all product versions.
Visualize operational dependencies
Furthermore, the 3D digital twin provides a structured visualization of task or operational dependencies, crucial for complex defense systems. By mapping out which tasks must be completed before others can begin, it ensures more efficient project management and resource allocation.
In air defense, where systems have numerous interconnected components, the precedence graph helps to identify potential bottlenecks, optimize workflows, and improve overall project schedules. It brings clarity to system development, troubleshooting, and operational readiness, ensuring that product-critical processes are executed in the correct order.
Enhance safety analysis
By providing a comprehensive virtual model of the entire system, engineers can perform detailed hazard assessments and simulate analyze operational scenarios to identify potential safety risks before they occur.
The digital twin allows safety-critical functions and emergency procedures to be analyzed in a controlled, risk-free environment. Integrating safety analysis into the digital twin framework not only improves the overall safety and reliability of the system but also ensures compliance with stringent defense industry safety standards. This proactive approach accelerates the certification process and builds greater confidence in the system's readiness for deployment in high-risk environments.
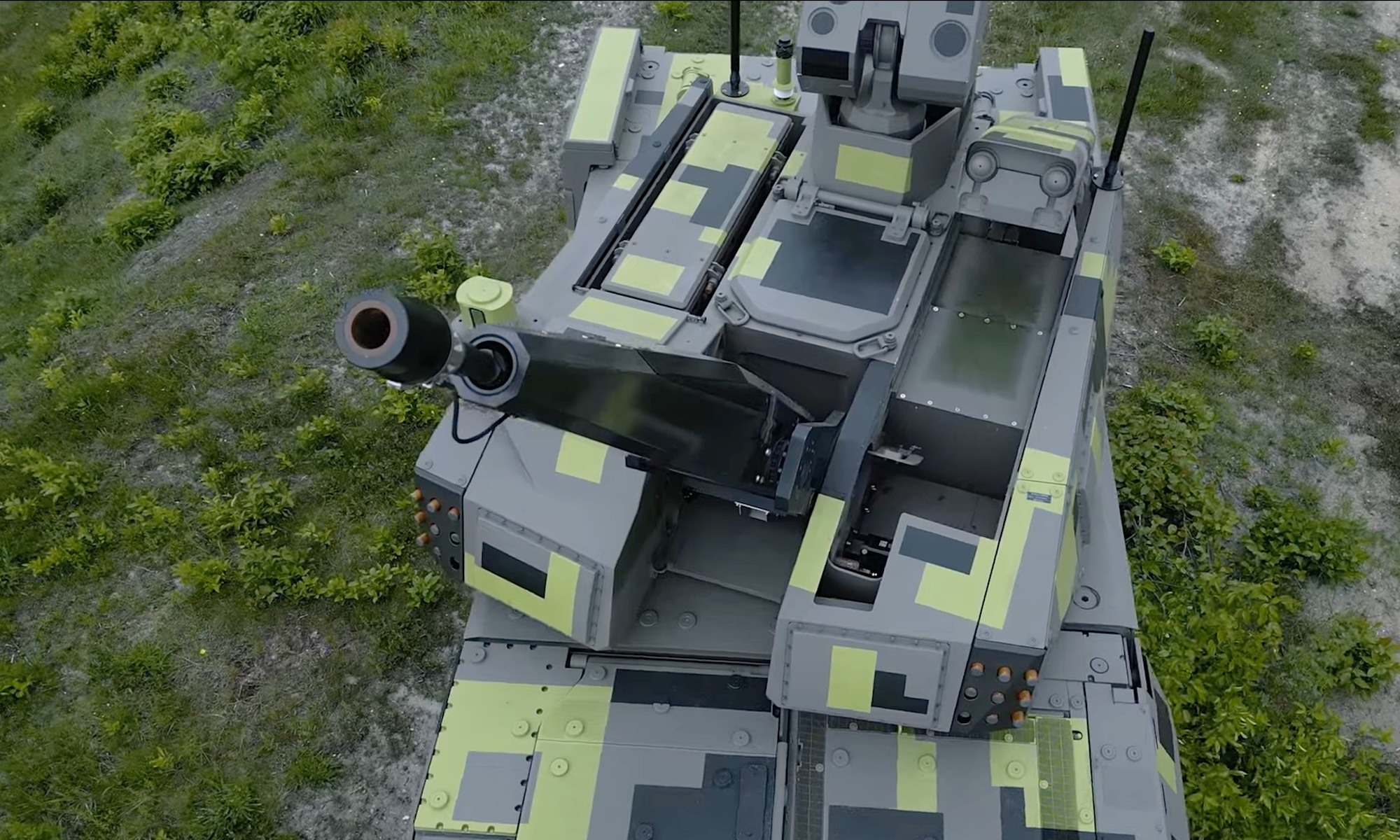
Defense Digital twin solutions– powered by SPREAD
We are of the innovative tech companies active in this space. While originally serving automotive customers with digital twin and Agentic Engineering Intelligence software solutions, we have built dedicated solutions for defense companies based on the same technology proven in automotive. SPREAD integrates data from diverse sources like PLM, PDM, and CAD systems through smart connectors, creating a dynamic, centralized view of complex systems that eliminates silos and ensures fast, reliable access to information.
Powered by a Knowledge Graph, the Product Twin consolidates and contextualizes product data, supporting simulations, dependency analysis, and role-based, secure access to sensitive information. The Action Cloud automates complex tasks like compliance checks and requirements optimization, empowering engineers to focus on innovation while ensuring precise, actionable insights.
By using advanced technologies such as knowledge graphs and machine learning to ensure seamless data integration and scalability, engineers are empowered to make data-driven decisions and implement improvements more effectively across production and R&D stages. Furthermore, SPREAD uses a precise data-sharing model which grants each user access based on their role, ensuring that only relevant data is available where and when it's needed. This approach is designed to protect sensitive information, maintain compliance standards and improve collaboration across teams. It ensures that engineers, managers, or external partners only have access to the data necessary for their specific tasks.
-1.png)
What’s next for the digital twin framework?
Integrating digital twin technology throughout the entire defense product lifecycle, from R&D through Production, Aftermarket, and maintenance, has the potential to revolutionize the way engineers design, develop and manufacture advanced air defense systems.
But that’s not all. AI agents that are trained on either domain knowledge or company data will play a pivotal role in driving further breakthrough innovation within the defense digital twin framework.
Such AI agents can facilitate real-time optimization of subsystems, dynamically adjusting parameters to ensure peak performance. They can simulate multiple scenarios, test how different variables interact within the system, allowing defense teams to explore new design possibilities and innovative configurations - without the need for physical prototypes.
They can also autonomously analyze vast amounts of real-time data from the digital twin, identifying patterns, anomalies, and potential system vulnerabilities that might be invisible to human engineers.
This dramatically reduces R&D time and costs while paving the way for novel defense solutions. By automating routine tasks, such as diagnostics and resource allocation, AI agents also free up engineers to focus on strategic, high-level innovation, pushing the boundaries of what’s possible in defense technology today.
Conclusion
By enhancing the physical system with its digital counterpart, SPREAD’s Defense Digital Twin solution fosters cross-functional collaboration while ensuring near real-time monitoring. This advanced approach accelerates production, enhances efficiency, and allows seamless updates, ensuring systems like the Skyranger remain at the forefront of defense capabilities.
For the Skyranger project, this approach not only means accelerated development and production but also enhanced efficiency and reliability. It enables seamless updates and adaptations, too, ensuring that the Skyranger remains at the forefront of defense capabilities - prepared to meet the evolving demands of modern challenges with precision and agility.