Closed-Loop Manufacturing: Can Digital Twins enhance innovation and efficiency in Production?
Short answer is: No! Because in this environment, traditional manufacturing systems with loosely connected design, production, and operations processes often fall short, as the demands of new technologies, stricter regulations, and shorter development cycles outpace the capabilities of linear approaches.
What are the limitations of siloed processes?
For Stefan Schmidt, a veteran Product Line Manager, every decision ripples across timelines, budgets, and market success. His role demands balancing the weight of innovation against the unforgiving constraints of cost, quality, and launch deadlines. Yet, despite meticulous planning, fragmented workflows and siloed data have repeatedly challenged his team’s ability to deliver flawless results.
- Delayed feedback: In a purely linear or “open-loop” environment, issues discovered during production or in-service may take months to filter back to the R&D and design teams.
- High risk of quality gaps: When production data isn’t continuously fed back, small flaws in materials or processes can compound into recalls or expensive rework.
- Fragmented data landscape: Product Lifecycle Management (PLM), Manufacturing Execution System (MES), and Enterprise Resource Planning (ERP) systems each have their strengths, but they are often used in isolation, limiting the ability to run holistic analytics or generate cross-functional insights.
Navigating these challenges, Stefan finds a transformative ally in Closed-Loop Manufacturing (CLM), a company-wide initiative that marked a significant cultural shift toward innovation and integration. Thanks to this strategic decision by his organization Stefan now benefits from a system that goes beyond standard condition monitoring and discrete engineering tools. It now ties the entire product lifecycle into one continuous feedback loop and empowers his team to tackle challenges with unprecedented agility and precision.
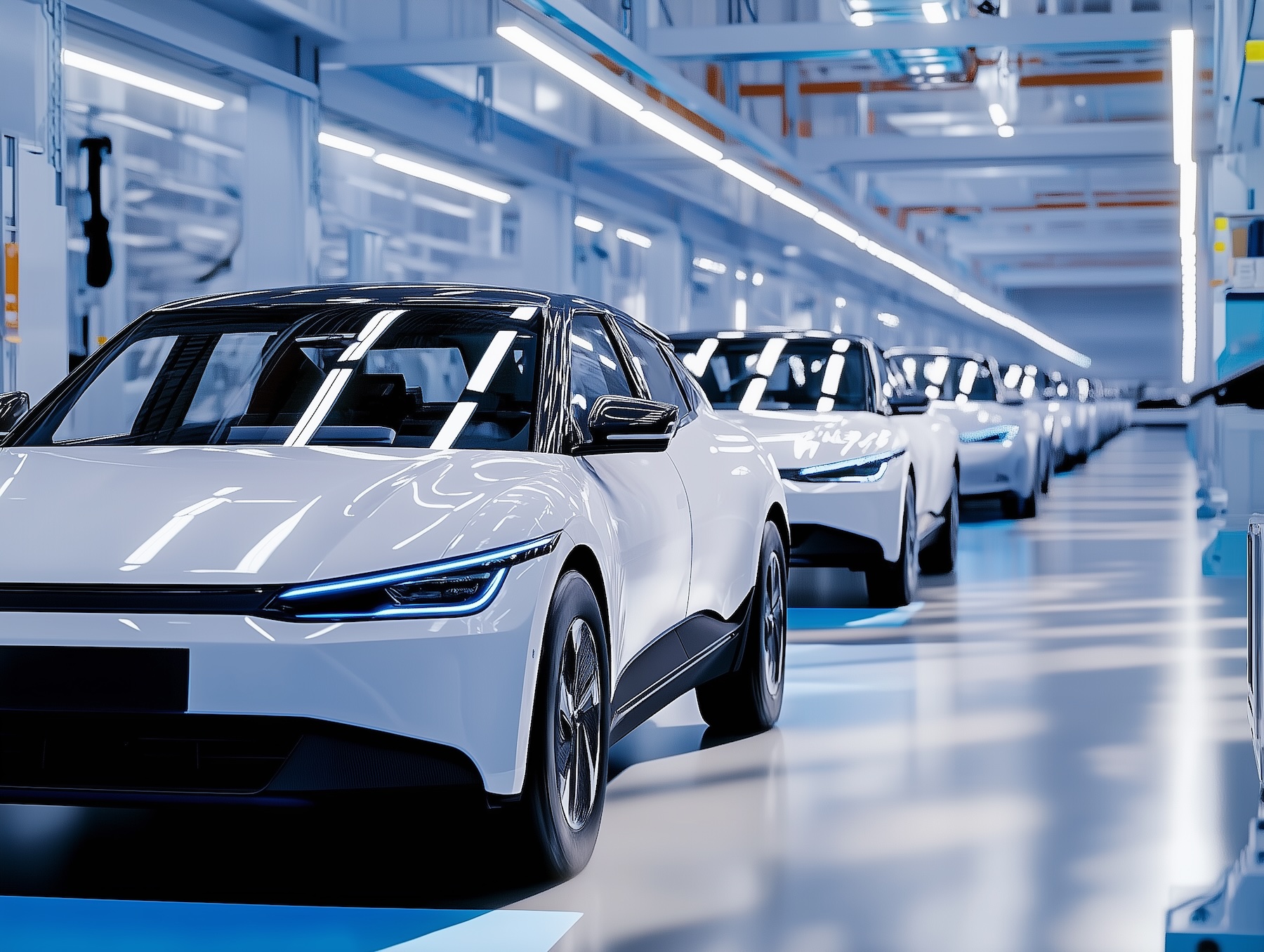
What is Closed-Loop Manufacturing (CLM)?
Closed-Loop Manufacturing creates a continuous feedback loop between the design, production, and real-world performance of a product. Central to this approach is the Digital Twin, a virtual replica of physical products, systems, or processes that bridges the digital and physical worlds.
Digital Twins enable teams to simulate, optimize, and monitor operations in real-time, drastically reducing inefficiencies and enhancing decision-making. For Stefan’s team, Digital Twins transformed their ability to address a critical EV battery cooling issue. What once took weeks to resolve was now completed in just two days, thanks to the insights provided by this technology.
Understanding the role of Digital Twins in CLM
Digital Twins are more than digital blueprints; they are dynamic, data-driven models that mirror the real-time conditions and behavior of their physical counterparts. By harnessing data from IoT sensors, manufacturing systems, product data and real-world usage, they empower manufacturers to:
- Simulate scenarios: Test products under diverse conditions—such as extreme weather or high-altitude performance—without physical testing.
- Optimize processes: Refine manufacturing workflows by analyzing real-time data for bottlenecks or inefficiencies.
- Increase quality: Identify product issues early and allow speedy error resolution especially when it comes to electric, electronical, and software failures
- Enhance predictive maintenance: Monitor machinery and equipment for early signs of wear or failure, avoiding unplanned downtimes.
- Drive sustainability: Identify waste and improve resource utilization to meet environmental goals.
In Stefan’s experience, integrating Digital Twins into the manufacturing lifecycle enabled his team to design, validate, and adjust scenarios collaboratively. In this context they e.g. enable detailed simulations, performance optimizations, comprehensive lifecycle management or real-time decision-making. By providing a centralized hub for real-time insights, Digital Twins empowered his team to make informed decisions that improved both product quality and production efficiency.
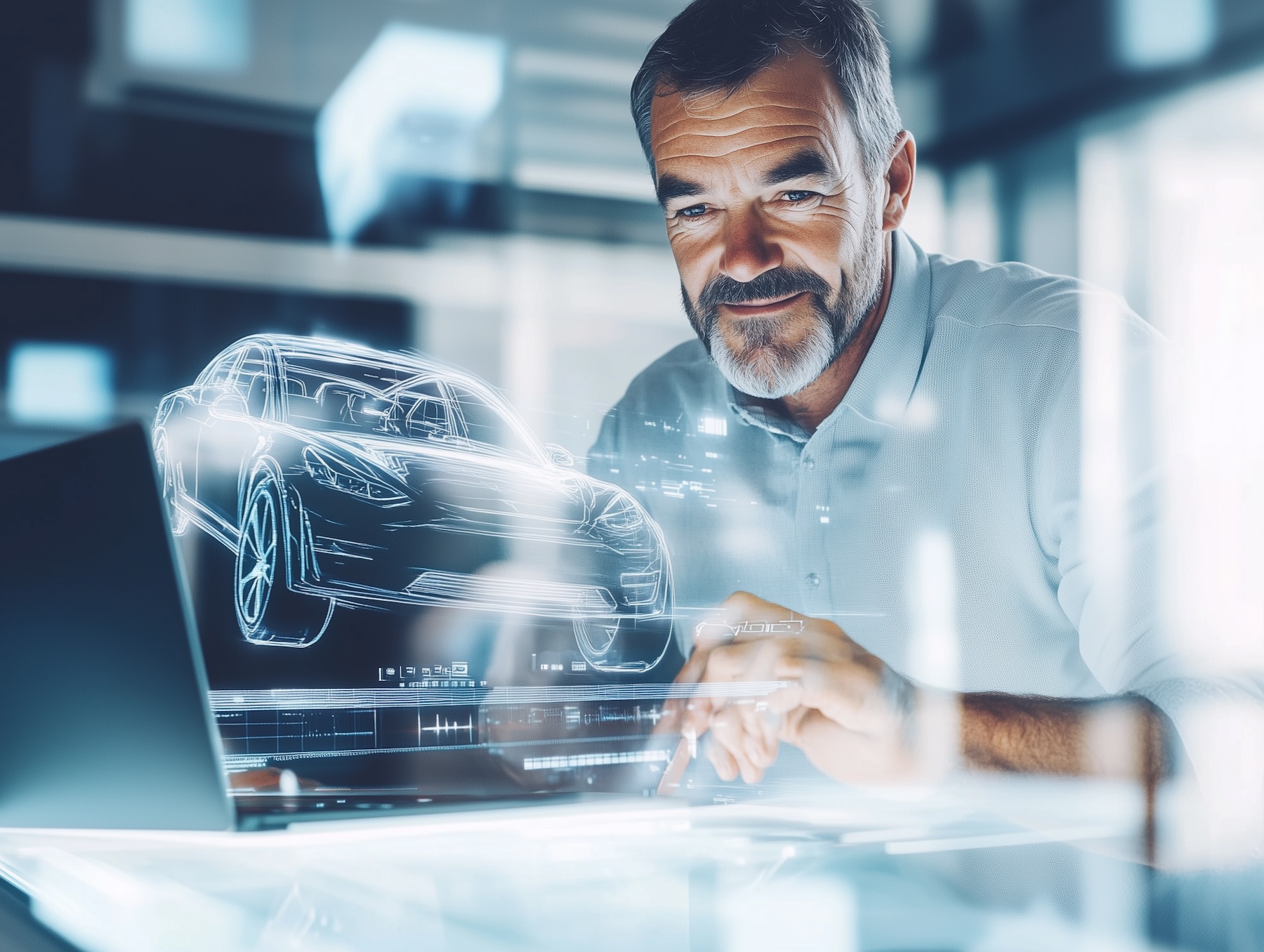
A day in the life of a Production Manager - now truly “closed-loop”
As a Product Line Manager, Stefan is juggling cost pressures, time-to-market deadlines, and quality demands. Before adopting CLM, Stefan was frustrated by lengthy communication loops between design, prototyping, and production. Problems discovered in testing took weeks to filter back to CAD teams, and machine operators rarely had real-time data on design changes.
Morning: Data-driven design refinement with immediate impact
Stefan starts his day with a CLM dashboard that aggregates data from multiple real-world sources—IoT sensors on the shop floor, supply chain metrics, and product & performance data from various systems in R&D.
A spike in warranty claims for a specific EV battery cooling line is instantly flagged. Instead of waiting for a scheduled project review, design engineers see the exact conditions causing coolant leaks and can adjust CAD models within hours.
Afternoon: Integrated Production tweaks with real-time response
Once the revised design is approved, CLM automatically pushes new assembly instructions – that have been derived instantly using precedent graph technology - to the Manufacturing Execution System (MES), ensuring that robotic assembly stations and foremen receive up-to-date welding parameters.
If the system detects a potential misalignment in a welding fixture, it sends an alert for immediate calibration. Production can continue with minimal downtime.
Evening: Full continuous improvement loop
The system logs any production anomalies in the PLM environment, feeding insights back into the design guidelines. This also triggers updates to the simulation model (Digital Twin) used for future design validations. By day’s end, engineering teams have more accurate data to plan product changes, and the loop continues seamlessly.
Stefan’s biggest relief? No more guesswork or blind assumptions; every design or process tweak is grounded in real, validated data.
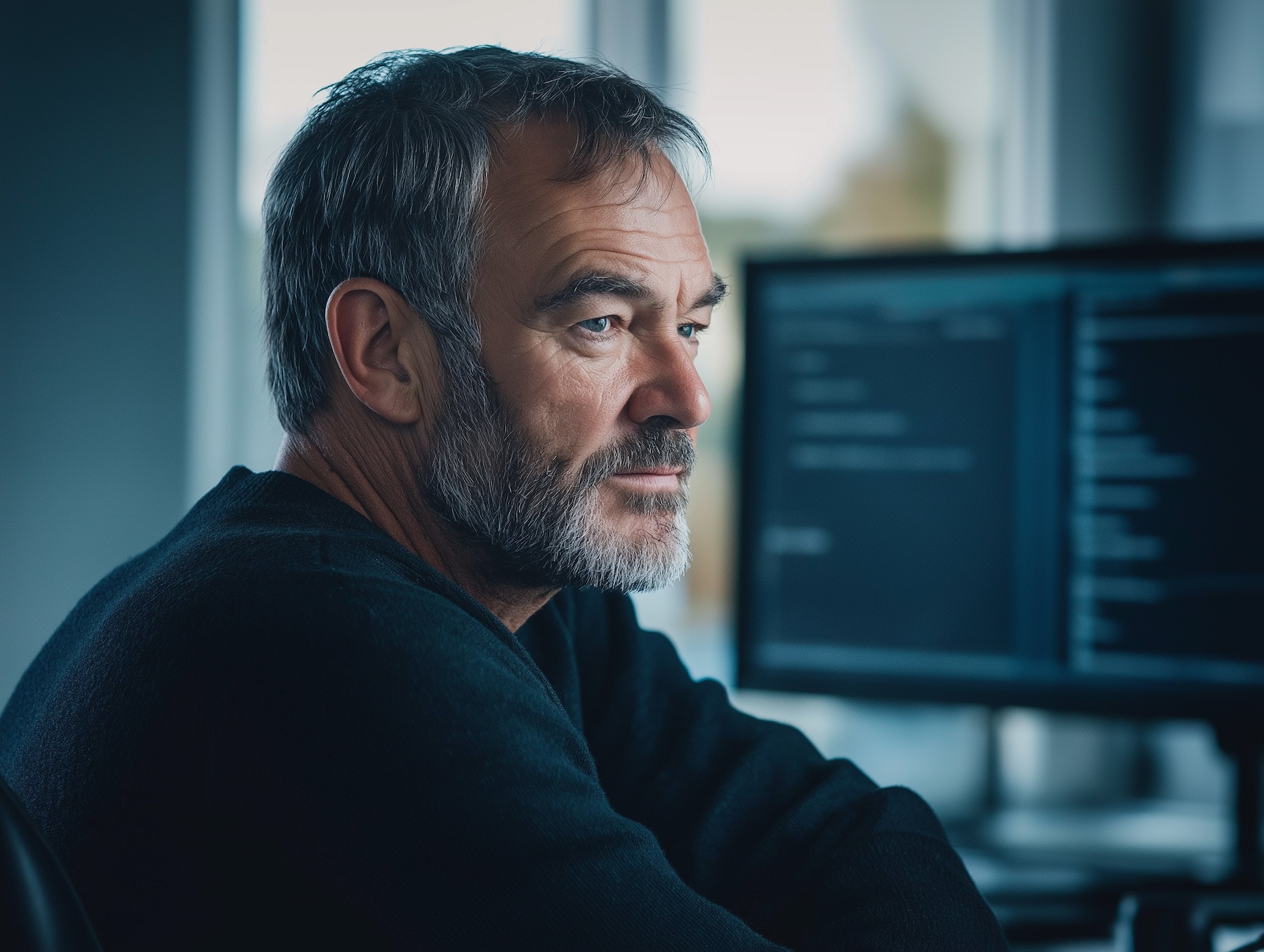
The four stages of Closed-Loop Manufacturing
CLM operates through four key stages, each building on the previous one to ensure continuous improvement:
1. Product data integration and traceability
Ensures seamless alignment between R&D and production, reducing errors and costly rework. For instance, Stefan’s team leveraged a Digital Twin to quickly identify and correct a design flaw in an EV battery cooling system, shortening the resolution time to just days.
2. Smart manufacturing and real-time adjustments
IoT-enabled systems enable real-time monitoring and adjustments, preventing delays. A miscalibration in a robotic welding station during pre-production was identified by the Digital Twin and corrected in real-time, preserving both timelines and quality.
3. Product and performance monitoring and Predictive Maintenance
Real-world product and performance data flows into Digital Twins, enabling teams to preemptively address issues. For example, Stefan’s team used Digital Twins to monitor axle temperature anomalies in prototypes, resolving issues before production began.
4. Feedback loops driving innovation
Data from real-world product use feeds back into design and manufacturing to enable continuous improvement. For instance, Stefan’s team identified wear patterns in suspension components, refining designs to reduce warranty claims and enhance durability.
Implementation deep dive: Data integration, security, and standards
Implementing CLM effectively requires more than just linking sensors and product data to the cloud. Key considerations include:
1. Data quality & Governance
- Ensure that data is accurate, standardized, and traceable. Poor data quality can create false flags or missed alerts.
- Deploy robust governance policies to decide how data is collected, cleaned, stored, and accessed.
2. System integration
- CLM typically interacts with PLM, MES, ERP systems, as well as supplier portals, digital twins, and analytics platforms.
- Choose integration approaches (APIs, middleware, or direct database connections) that minimize manual data transfer and reduce risk.
- Knowledge Graph technology proves to be a key enabler to create domain specific semantic models contextualizing the data and deriving actionable information in the users’ specific context
- Also they provide the base for meaningful usage of AI models and agents
3. Security & IP protection
- Real-time data exchange raises security concerns. Encryption, role-based access, and secure data pipelines are crucial—especially in automotive and aerospace, where intellectual property can be highly sensitive.
- Compliance with industry-specific standards (e.g., TISAX in automotive, DO-326A / ED-202A in aerospace) may be necessary.
- Standards alignment (IATF 16949, EN 9100, etc.)
- CLM supports traceability requirements in these standards by ensuring that each product’s digital twin updates automatically from design through to in-field service data.
- Automated documentation generation can help satisfy audits and quality checkpoints faster than manual reporting ever could.
4. Standards alignment (IATF 16949, EN 9100, etc.)
- CLM supports traceability requirements in these standards by ensuring that each product’s digital twin updates automatically from design through to in-field service data.
- Automated documentation generation can help satisfy audits and quality checkpoints faster than manual reporting ever could.
5. Organizational culture & processes
- Implementing CLM often requires changes in team roles and collaboration workflows. Cross-functional cooperation is key to ensure that design, production, quality, and service teams all speak a common “data language.”
Hard facts and KPIs: Quantifying the value of CLM
Implementing Closed-loop Manufacturing (CLM) brings a multitude of benefits that transform how manufacturers operate.
While every organization’s baseline differs, common metrics that improve under CLM include:
- Time-to-market reduction: By up to 20–40%, thanks to accelerated design validation and fewer late-stage changes.
- Quality improvements: 30–50% drops in scrap or rework rates due to earlier detection of design or production flaws.
- Predictive Maintenance ROI: Equipment downtime often cut by 25–50% through proactive scheduling and design updates to address recurring failures.
- Warranty claim reduction: Potential decrease of 10–30% from real-time field feedback that drives targeted design improvements.
Open Loop vs. Closed Loop: Comparison at a glance
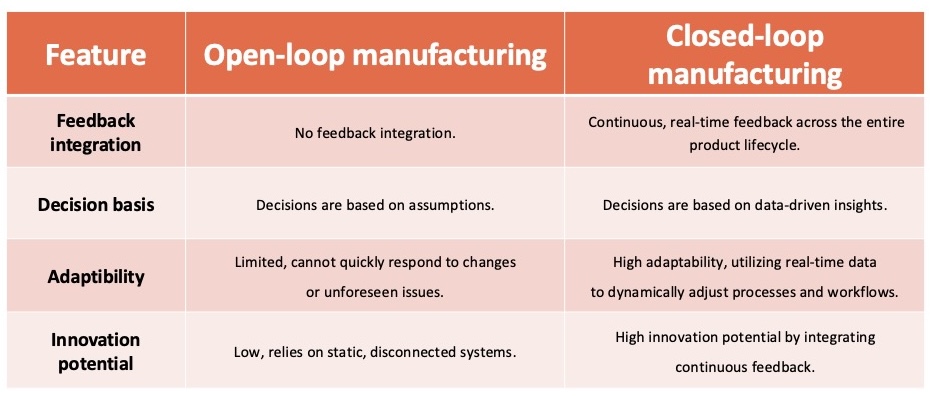
CLM vs. PLM, MES, APQP, and Digital Thread
Professionals often ask: “Is CLM just PLM or MES with a new name?” The short answer is no! It rather builds on these systems rather than replacing them.
- PLM (Product Lifecycle Management): Manages product data from concept to disposal, focusing on documentation, revision control, and collaboration. CLM leverages PLM data but ensures real-world performance metrics continuously update product definitions and design rules.
- MES (Manufacturing Execution System): Oversees production-floor operations like scheduling, dispatching, and resource utilization. CLM consumes MES data (e.g., cycle times, scrap rates) to refine design parameters, while simultaneously pushing design changes back into MES instructions.
- APQP (Advanced Product Quality Planning): A structured method (especially in automotive) for ensuring product quality from early design to production. CLM brings real-time field feedback into APQP phases to proactively address quality issues.
- Digital Thread: Refers to the seamless flow of data throughout the entire lifecycle. CLM is an application of the Digital Thread concept that specifically targets closed-loop feedback for continuous product and process optimization.
In short, CLM unifies and orchestrates data flows across all these systems, ensuring they function as part of a continuous, improvement-driven loop.
What's the difference between CLM and Predictive Maintenance?
It’s also tempting to think of Closed-loop Manufacturing as simply another layer of predictive maintenance, but CLM is broader. Condition-based or Predictive Maintenance typically focuses on monitoring equipment health to anticipate failures (e.g., vibrations, temperatures).
Closed-loop manufacturing goes one step further: it feeds those operational insights all the way back into engineering, R&D, and manufacturing planning. Product designs and process parameters are constantly fine-tuned based on real-world data, enabling iterative improvements throughout the entire lifecycle.
For example, a condition-monitoring system might send an alert that a robotic welding arm is nearing failure. But in CLM, that alert not only triggers maintenance; it also informs design engineers to tweak weld geometry or materials for future models, while simultaneously updating manufacturing execution parameters.
Beyond the present: Future trends in CLM
Closed-loop Manufacturing is more and more moving toward self-adapting systems, where AI algorithms continuously refine both design and manufacturing parameters in real time. As more factories adopt 5G networking and edge computing, the latency between sensing an issue and executing a corrective action will shrink further.
This paves the way for adaptive manufacturing lines where machines reconfigure themselves based on minor design changes or shifts in demand. It also allows machine learning models to detect and predict problems, as well as identify new design opportunities. These models provide complete tracking of products, enhancing transparency and enabling real-time assessments of a product's carbon footprint, material use, and recyclability.
Conclusion: The future of manufacturing is closed-loop
For manufacturers in the automotive and aerospace sectors, CLM is a tangible, data-driven strategy that integrates sensor feedback, production metrics, and real-world performance into a single continuous feedback loop. By closing the gap between engineering and operations, organizations can rapidly adapt to challenges, meet strict quality standards, and drive relentless innovation.
In Stefan Schmidt’s world, the days of waiting on sporadic feedback and siloed updates are over. Now, real-time data flows seamlessly between design and production, and every improvement in the field fuels the next wave of product innovation. This is the power of Closed-Loop Manufacturing—and it’s shaping the future of how we design, build, and optimize products in the most demanding industries on the planet.
Transform your manufacturing with SPREAD
At SPREAD, we bring this vision to life. Our Agentic Engineering Intelligence solutions combine advanced analytics, real-time data integration, and industry-specific expertise to deliver measurable results. Let us help you stay ahead in this competitive landscape. Connect with us today to transform your manufacturing processes into a future-proof advantage.
Discover how SPREAD can revolutionize your manufacturing processes with:
- Customized digital twin solutions: Designed to meet your specific industry needs.
- Advanced analytics and AI integration: Utilizing the latest in machine learning for informed decision-making.
- Seamless system integration: Ensuring all stages of your manufacturing lifecycle work together smoothly.
Learn more about how our innovative solutions can improve your production environment, boost efficiency, and keep your business at the forefront of manufacturing excellence.