The Swedish King & sustainability along the product lifecycle: a royal technology mission at SPREAD
The IVA — the Royal Swedish Academy of Engineering Sciences — came by SPREAD and brought along a very special guest. We had the honor of hosting the King of Sweden, H.M. King Carl XVI Gustaf, along with a delegation of 40 representatives of industry, government, and academia. The visit was part of the IVA’s 26th annual Royal Technology Mission — a tour of innovative companies with the purpose of bringing together leaders to exchange knowledge about the technologies shaping the future.
The theme at SPREAD: sustainability along the product lifecycle.
In particular, pinpointing how we can reduce the environmental footprint at each phase of the lifecycle by expanding the knowledge footprint within an organisation. Although sustainability is quite often associated with the limitation & and regulation of industry, our thesis is that a sustainable future requires bold, collaborative engineering innovation.
Innovation lives from the flow of knowledge. Right now, the way engineering knowledge flows in manufacturing organizations is slow and siloed — i.e., they have a small knowledge footprint. This leads to a lot of waste: wasted resources, wasted effort, wasted opportunities to make products more sustainable.
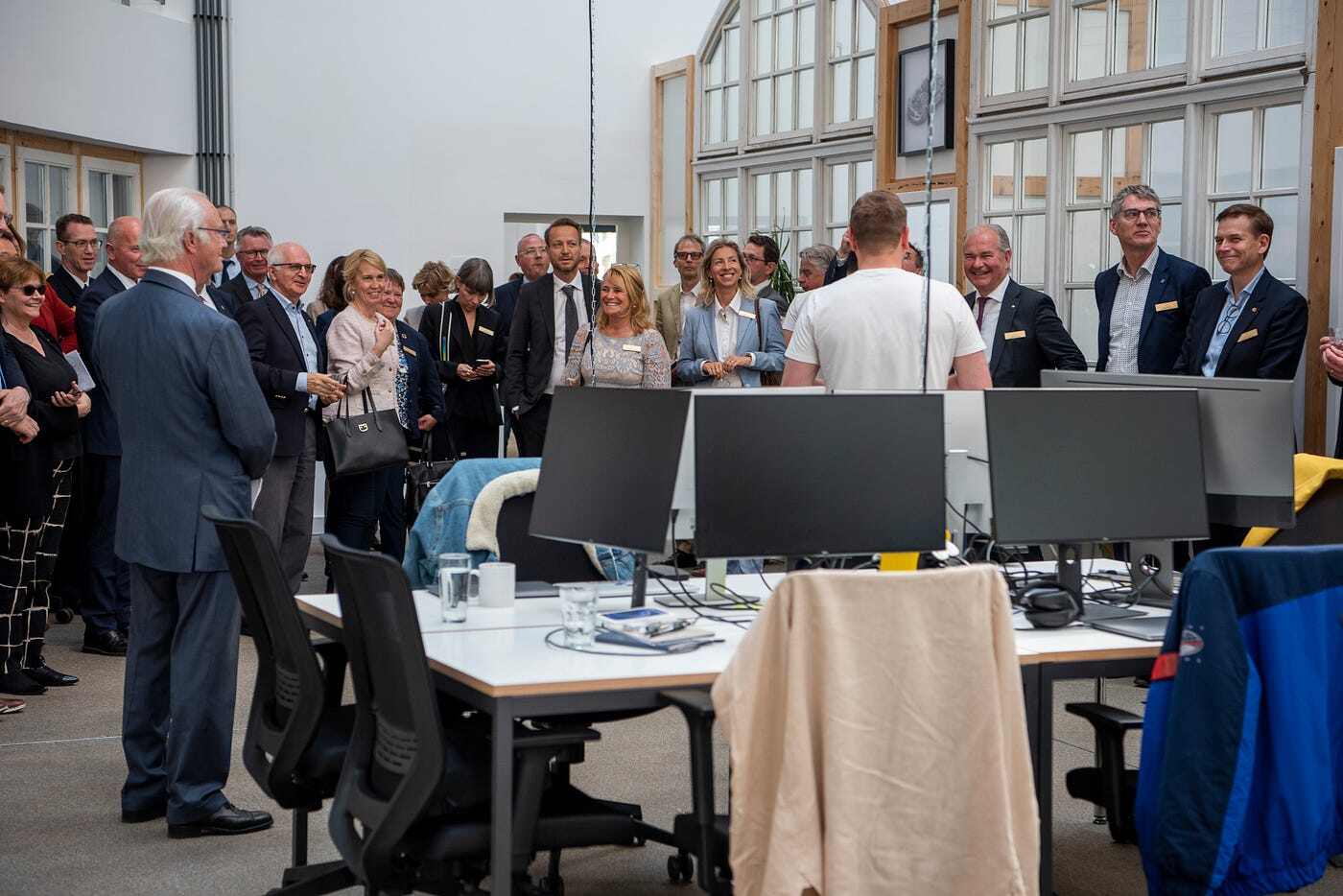
The goal is Net Zero.
There’s immense potential to reduce the environmental footprint in manufacturing and transportation to complement renewables, carbon capture, and electrification. The challenge with complex connected hardware products — like cars — is that, by the sheer complexity of their mechanical, electrical, and software dimensions, that potential remains hidden.
Our CTO & resident Swede, Tomas, explained our approach: create an Engineering Intelligence Graph out of existing product data. To enable organizations to connect and scale their engineering knowledge in 3D, and make it instantly available to every engineer across the product lifecycle. To create a platform that, with the help of AI, can serve as a single source of truth for any product — regardless of their complexity. An intelligent graph that keeps learning from each interaction, to provide companies with insights from their own data, so they can create the most innovative and sustainable products possible.
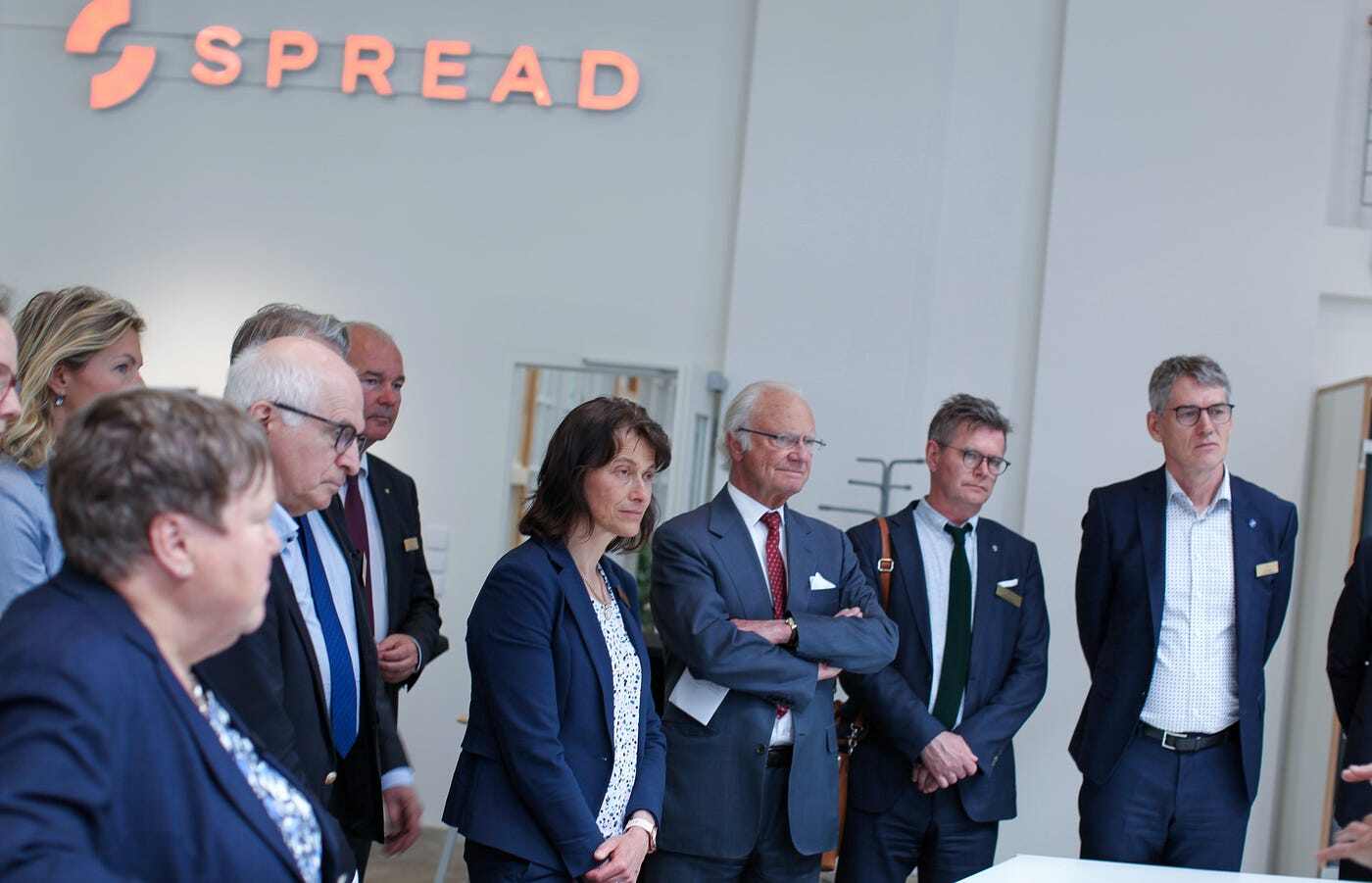
We wanted to show H.M. the King and the IVA how a holistic Engineering Intelligence Graph can contribute to sustainability efforts across the product lifecycle. The delegation attended three short sessions, where our team showcased applications of engineering intelligence in R&D, Production, and Aftersales, and saw concrete examples of how our customers reduce waste, manage complexity, and promote circularity at scale.
Here’s what they learned:
R&D: Weight reduction through optimizing wiring harness design can save as much CO2 as 12 million flights between Berlin and Stockholm
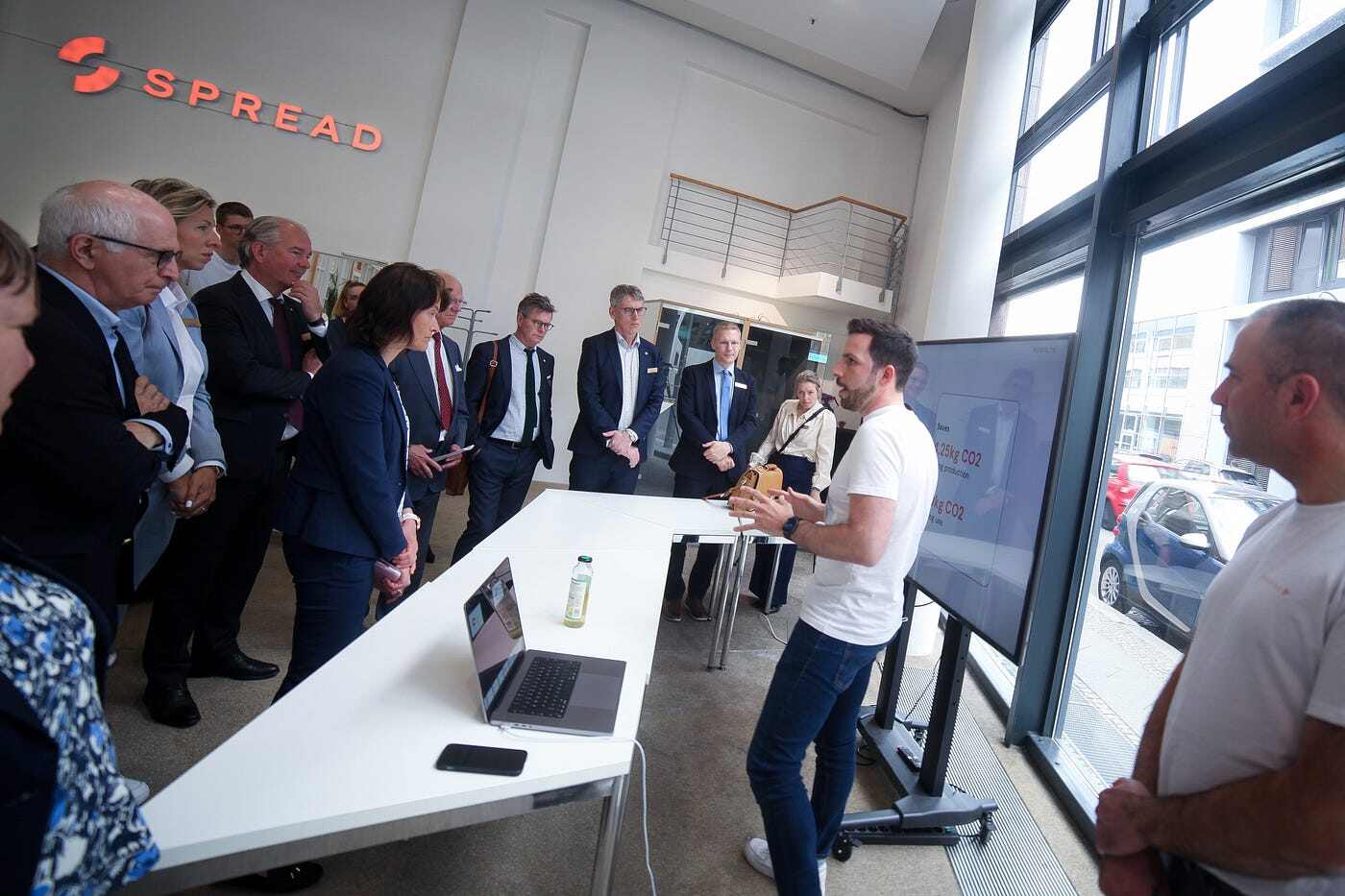
For every product, 80% of its total lifecycle emissions are decided in the design phase. With products as complex as today’s vehicles, there are lots of departments and countless engineers involved in that process. What these engineers lack is a tool that supports the communication between these different teams, each working on their own highly specialized piece of the puzzle.
Putting all the pieces together often means the engineering requirements and the physical design are incompatible. This leads to a game of iteration ping pong with cost-intensive change requests. Even worse, sometimes faulty designs make it into Production, and if the system doesn’t work as expected, it can lead to recalls. The lack of transparency also means there’s a lot of untapped potential to make the designs more cost- and resource efficient.
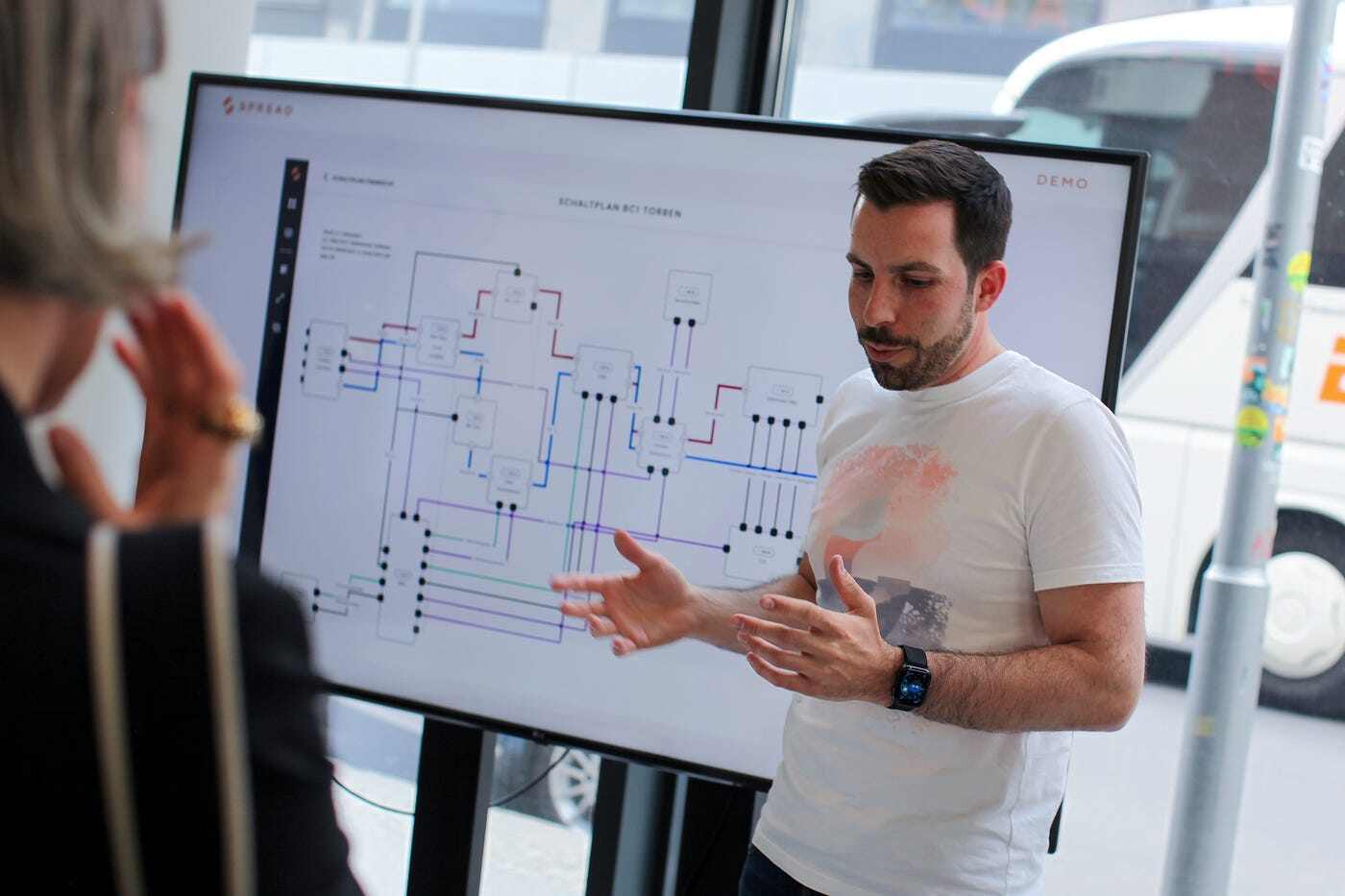
Freddie, our Head of Product, gave an overview of how wiring engineers in R&D can leverage a three-dimensional understanding of a vehicle to optimize a product and virtually validate its design. We showed attendees how SPREAD’s engineering intelligence platform creates a holistic understanding of the whole system by abstracting all the available product data: technical requirements, wiring data, CAD models, 2D diagrams, etc. This understanding then led to the insight that the wiring harness could be designed more efficiently, leading to a weight reduction of 1kg per series vehicle.
Saving 1kg of copper per vehicle means saving roughly €10 — or 4.25 kg CO2 during production, and 30 kg CO2 during the use phase. Consider roughly 80 million vehicles were produced in 2021: if we can make each one just 1kg lighter, that means preventing 2,730,000 tons of CO2 from being released into the atmosphere every year. That’s the equivalent of 12 million flights between Berlin and Stockholm.
If you take into account Sweden’s rank as the second most sustainable country in the world according to the Sustainable Development Report (SDR), you make sure to double check your CO2 calculations. Luckily, none of the professors of sustainability in attendance contradicted our numbers, so the groups went on to the next session.
Production: Error prevention & analysis with 3D knowledge graphs to increase quality
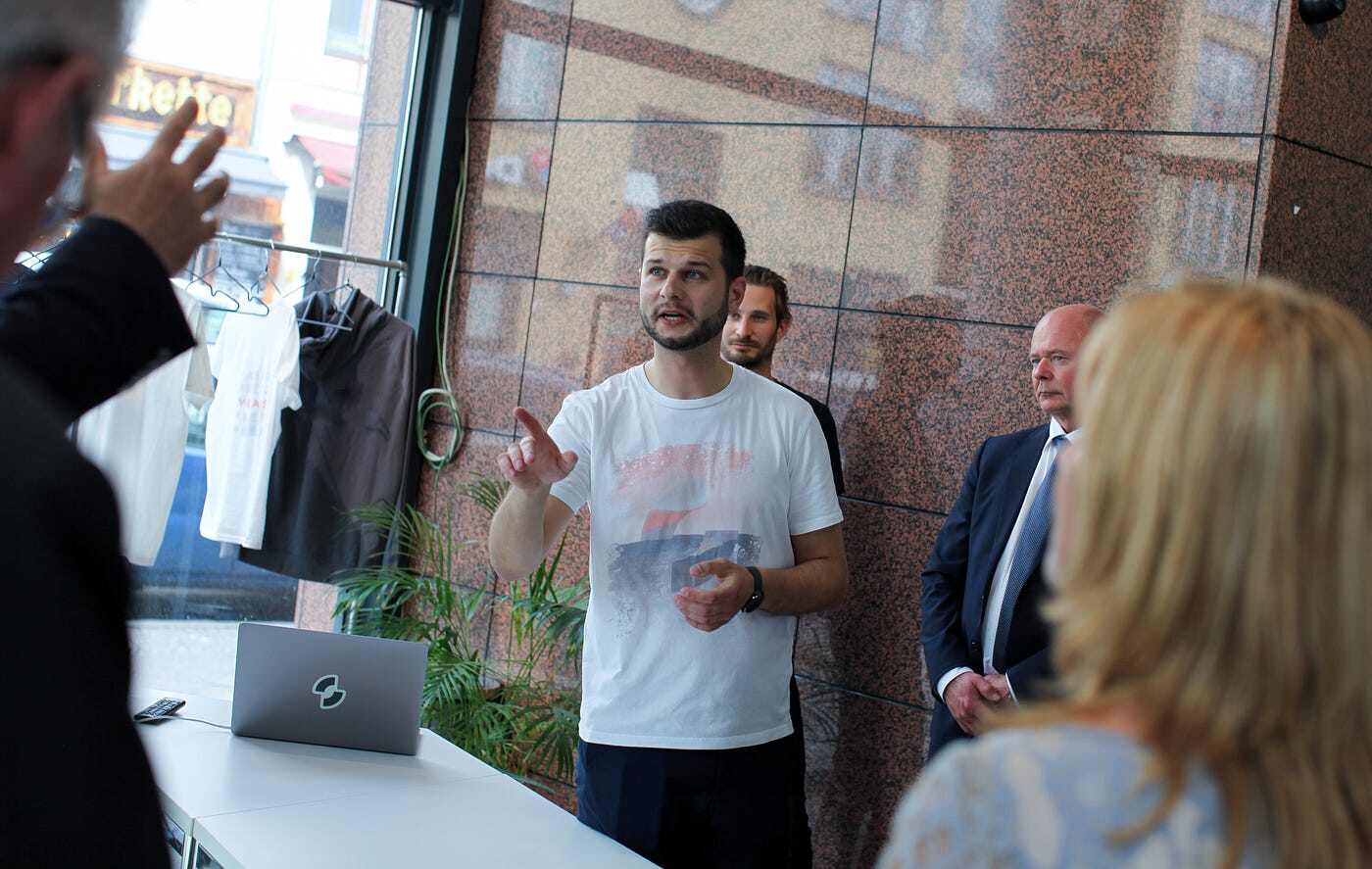
Product complexity affects and increases organizational complexity. With today’s cars becoming more complex as a product, car manufacturers are becoming more complex as an organization. New departments emerge, and with them, new silos. Connecting and spreading engineering intelligence across products, processes, and silos is an enormous challenge.
Symptoms of this complexity can be observed very clearly in the Production phase. Technicians are often confronted with unknown electric errors in this high-pressure environment, which they must resolve with impractical and unintuitive tools, like 18,000-page long PDFs with 2D diagrams. This makes the identification of errors extremely frustrating & time consuming.
It also means that fixing those errors requires a lot of guesswork and manual trial and error, which leads to a lot of preventable waste. To avoid stopping production at all costs, cars can spend hours in the rework area. In the worst cases, sometimes even brand-new cars are scrapped entirely if critical communication errors cannot be fixed.
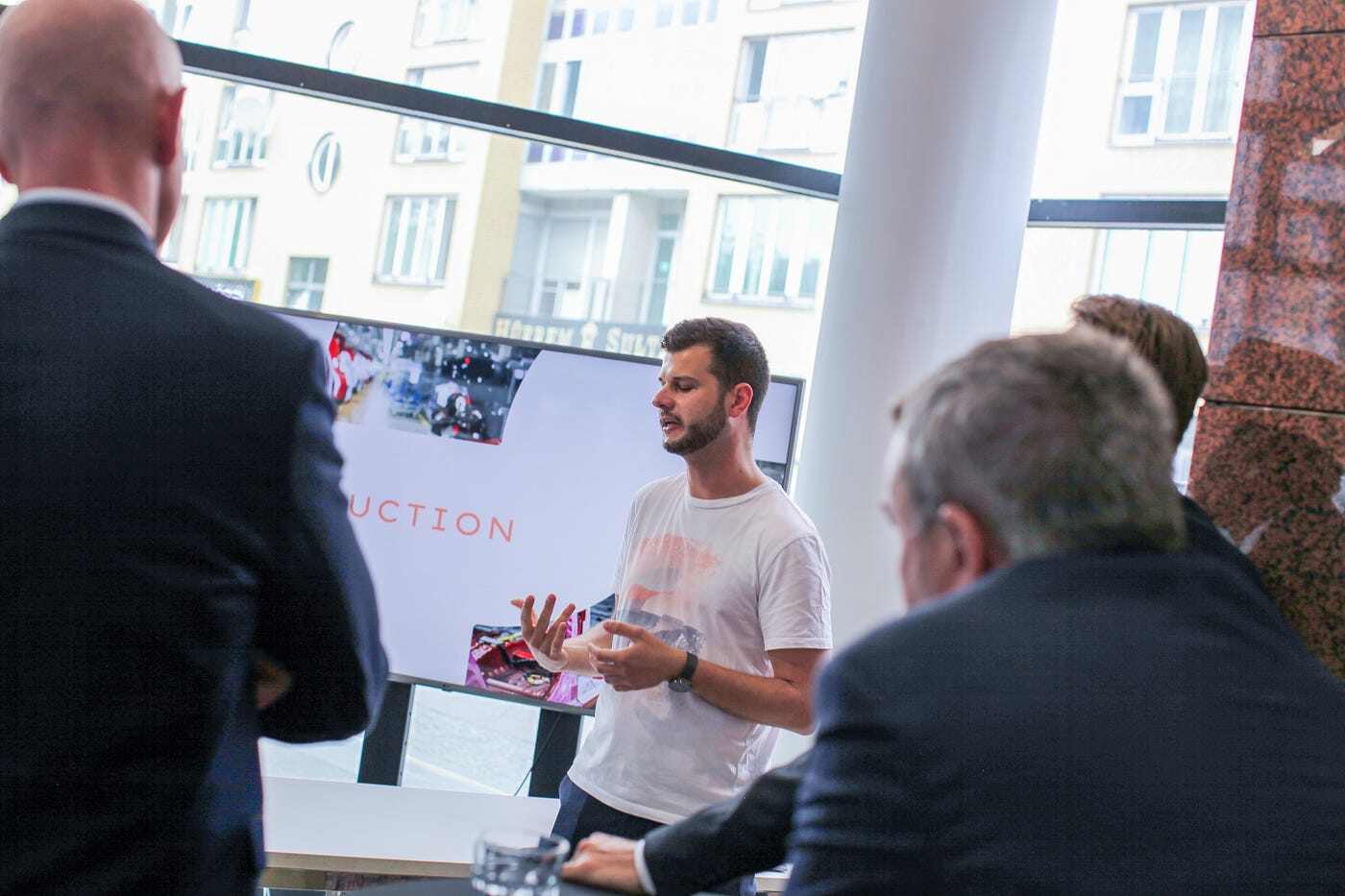
Production thus represents a crucial piece of a holistic approach to creating sustainable products. Thomas, our Product Manager, explained how you can connect the knowledge silos and gain a holistic understanding of the product complexity. An Engineering Intelligence Graph that combines 3D models, wiring and component data from R&D, with inputs on errors and configurations from Production, lets technicians conduct a 3D VIN-specific analysis and localization of failures, so cars can be reworked much faster.
Thomas showed us how, in practice, this faster rework method leads to savings of €1 million per assembly line. But there’s also the indirect effects — preventing errors in Production vs reacting to them later means higher quality vehicles on the streets. Higher quality vehicles means they have longer lifecycles, as well as happier customers.
Aftersales: Promoting circular economy by helping customers fix first & fast
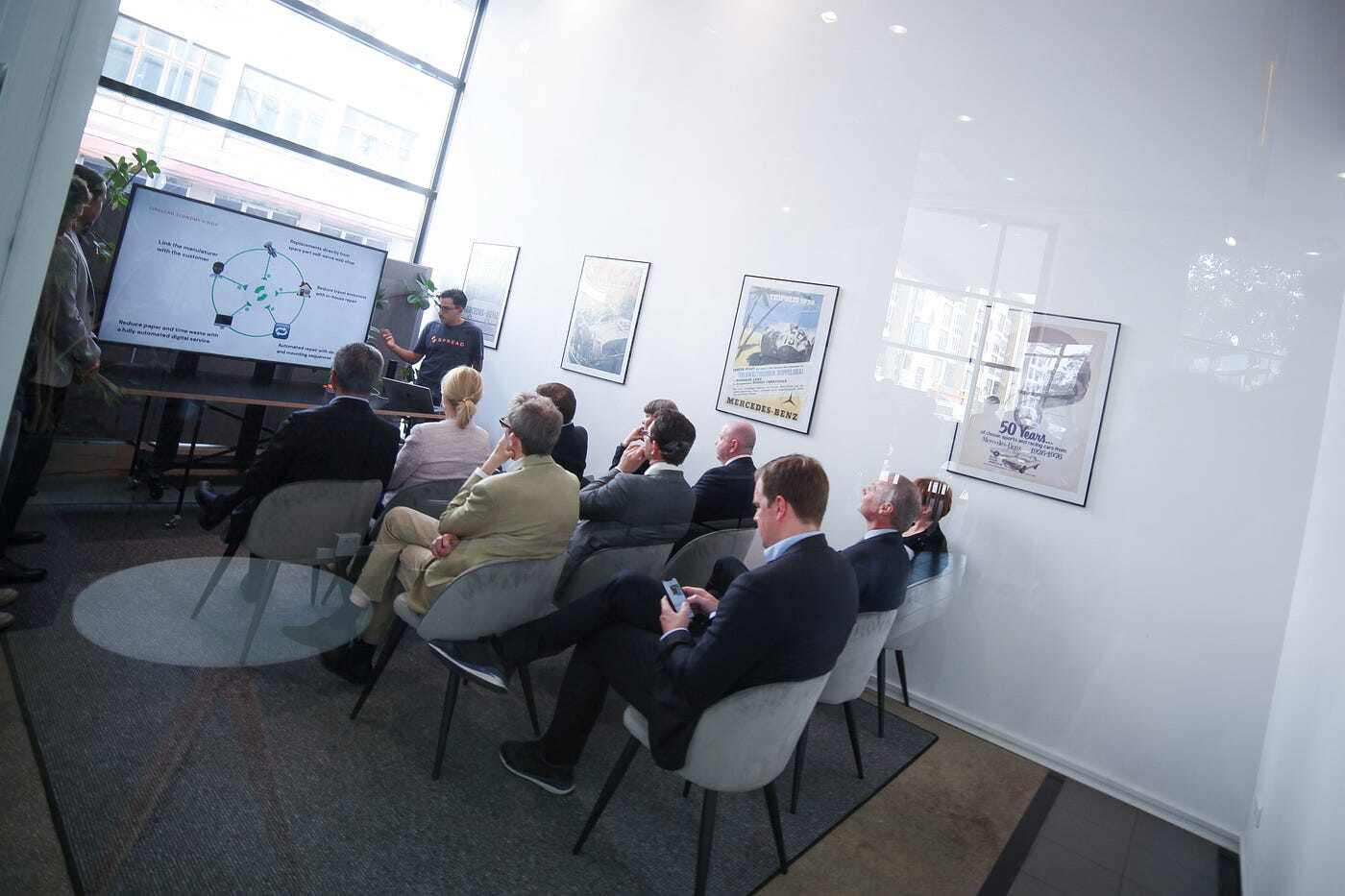
Picture this: your washing machine breaks down. You don’t know why exactly, so you call the manufacturer. They offer to send one of their experts for €300 an hour, plus the cost of travel and the replacement parts. I doubt anyone would opt for the sustainable ‘fix first’ option when a brand-new washer only sets you back €200.
The European Commission’s Right to Repair initiative mandates that all manufacturers must make repair instructions available to end users. But even with that information available in a manual with 2D diagrams and parts lists, it might not be digestible or practical for laypeople.
Moreover, when a large industrial machine needs maintenance or repair, they require technical expertise that might not be transferable from a PDF with diagrams. Even if it’s just a small part that can be easily replaced, the task can cause weeks or months-long downtime, which can be very expensive.
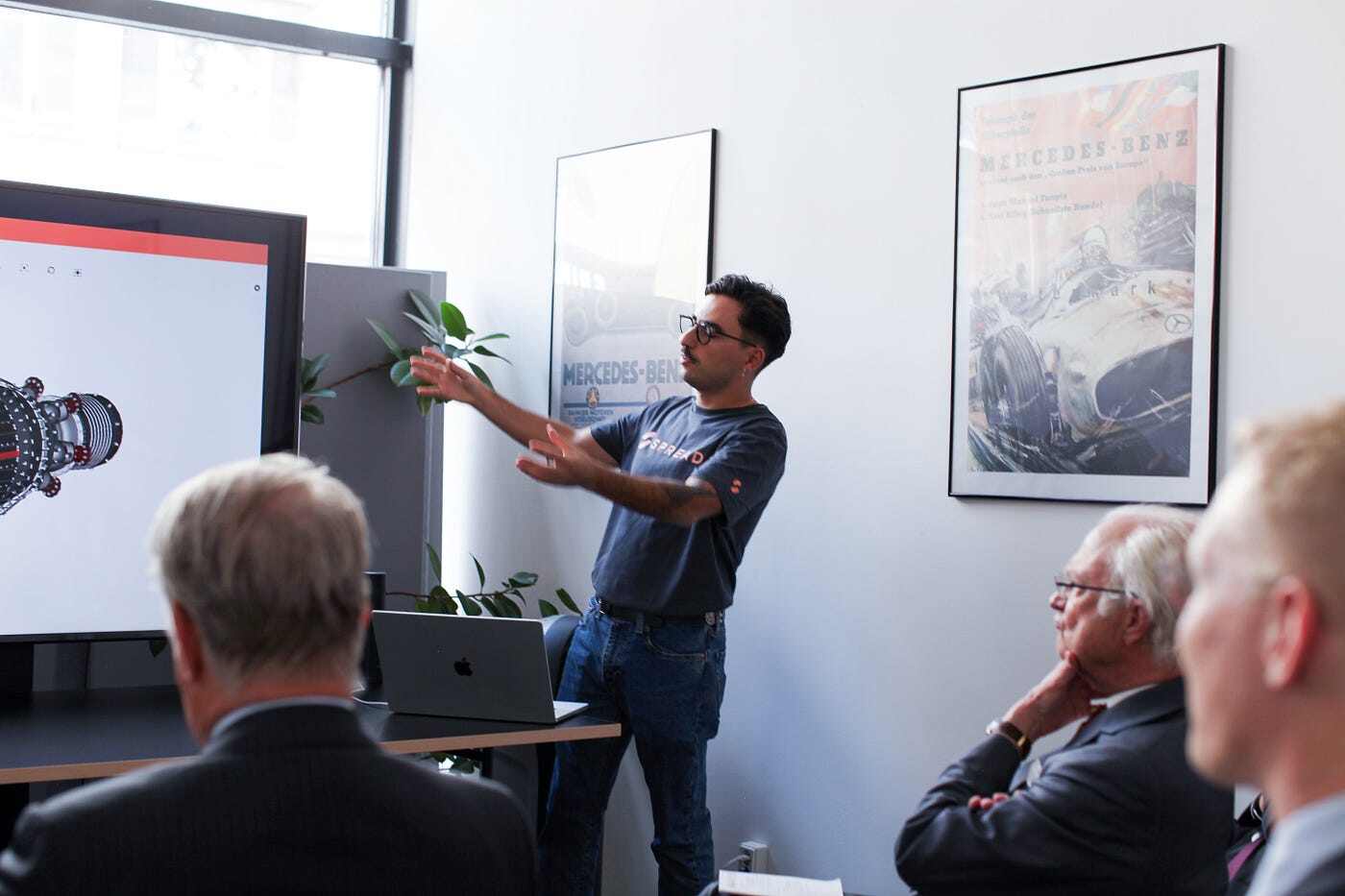
There’s still a significant knowledge (and thus skill) gap between manufacturers and consumers. We know that the data requires is already created in the design & assembly phase. João and Matthew showed us how, just by analyzing the CAD models, we can easily identify parts and link them with PLM data.
From the database, we can compare parts for classification and inventory, making it easy to reorder the replacement parts needed. By connecting data from Planning & Production, we can identify faulty parts and in which sequence to disassemble and reassemble the product with its replacement.
Our approach is simple: to connect the manufacturer with the consumer via a product’s Engineering Intelligence Graph. Doing so creates an intelligent inventory system in which manufacturers can directly ship replacement parts to the consumer. Through intuitive repair animations, it also increases efficiency and reduces waste, making the sustainable option easy and accessible for both manufacturers and consumers. Our goal is to make it cheap, easy, and fast to opt for circular economy.
Our vision: the exponential growth of the world’s engineering intelligence

Innovation and complexity go hand in hand: to create the sustainable products of the future, manufacturers must find a way of managing a product’s complexity. And the only way for organizations to master the growing complexity is with a shared, holistic, and intuitive graph of Engineering Intelligence.
There’s a strong relationship between an organization’s knowledge footprint and their environmental footprint. In this case, there’s a negative correlation: the larger the knowledge footprint, the lower the environmental footprint. For us at SPREAD, the goal with our applications is to enable customers to leverage their collective Engineering Intelligence, so they can accelerate development cycles, eliminate millions in inefficiencies, and reduce their environmental footprint at scale.
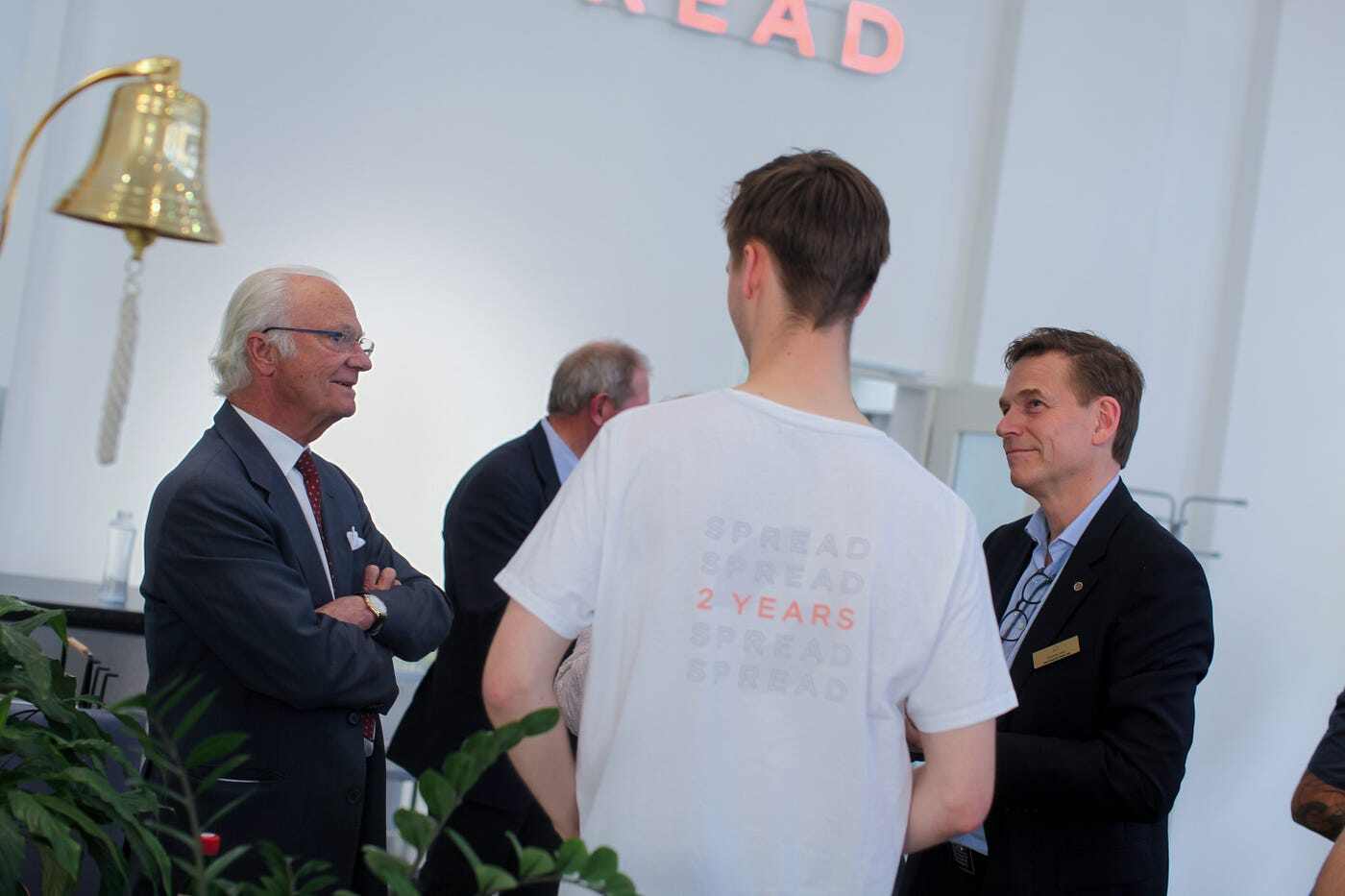
The Swedish King and the IVA delegation were excellent guests, asking thoughtful questions and engaging in meaningful discussion throughout their 90 minutes at SPREAD. They asked thoughtful questions about the technical aspects of expanding their knowledge footprint along the three benchmarks from R&D, Production and Aftersales.
That afternoon, the Royal Technology Mission demonstrated the only way to Net Zero: academia, government, industry, and individuals collaborating toward that common goal. Taking different approaches in harmony toward a joint purpose. We at SPREAD are incredibly proud to have been a part of it.
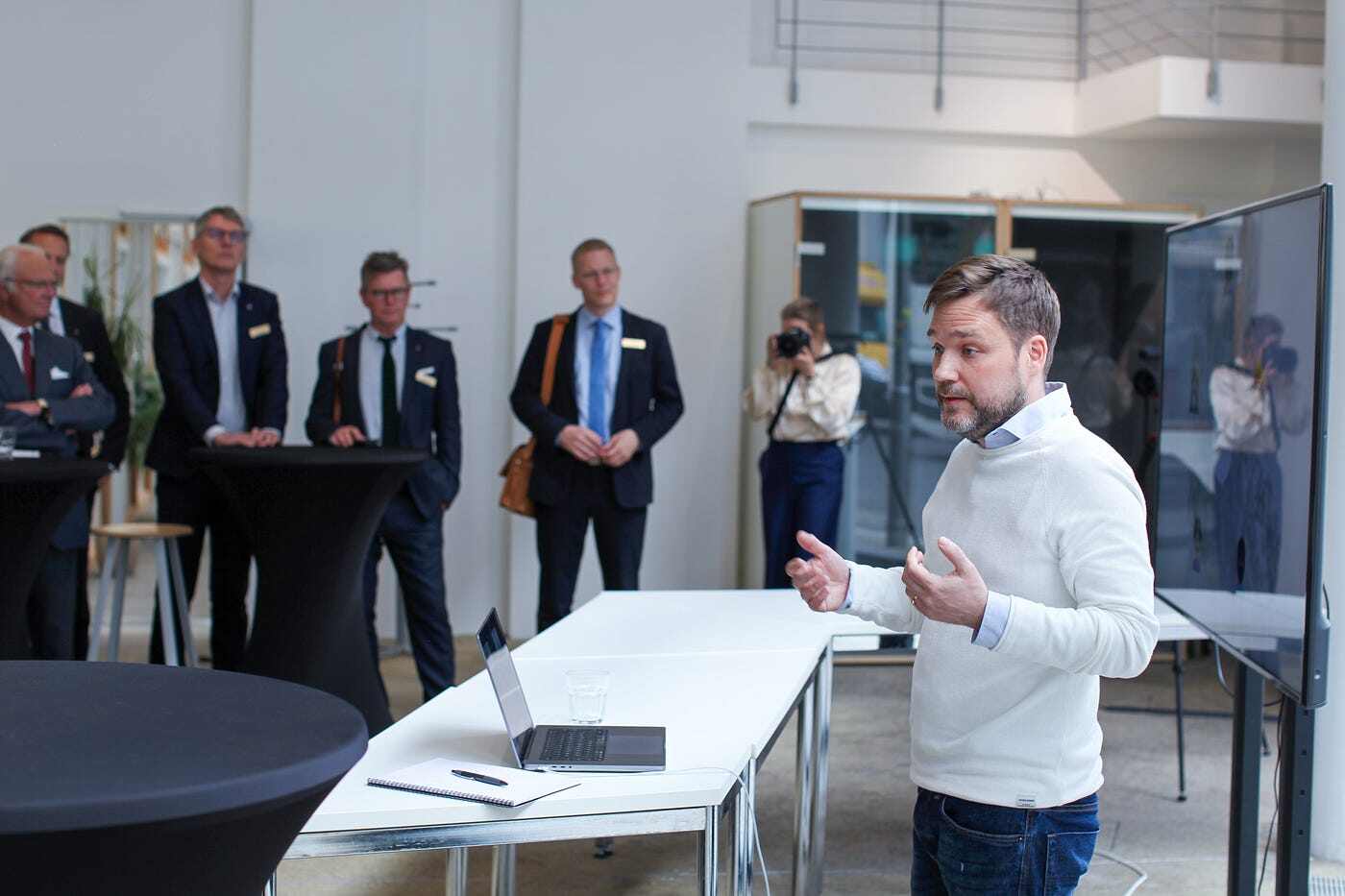