Resolve recurring E/E issues with system insights
Trace errors to system dependencies, uncover recurring patterns, and resolve E/E issues faster, reducing downtime and improving service quality.
Get started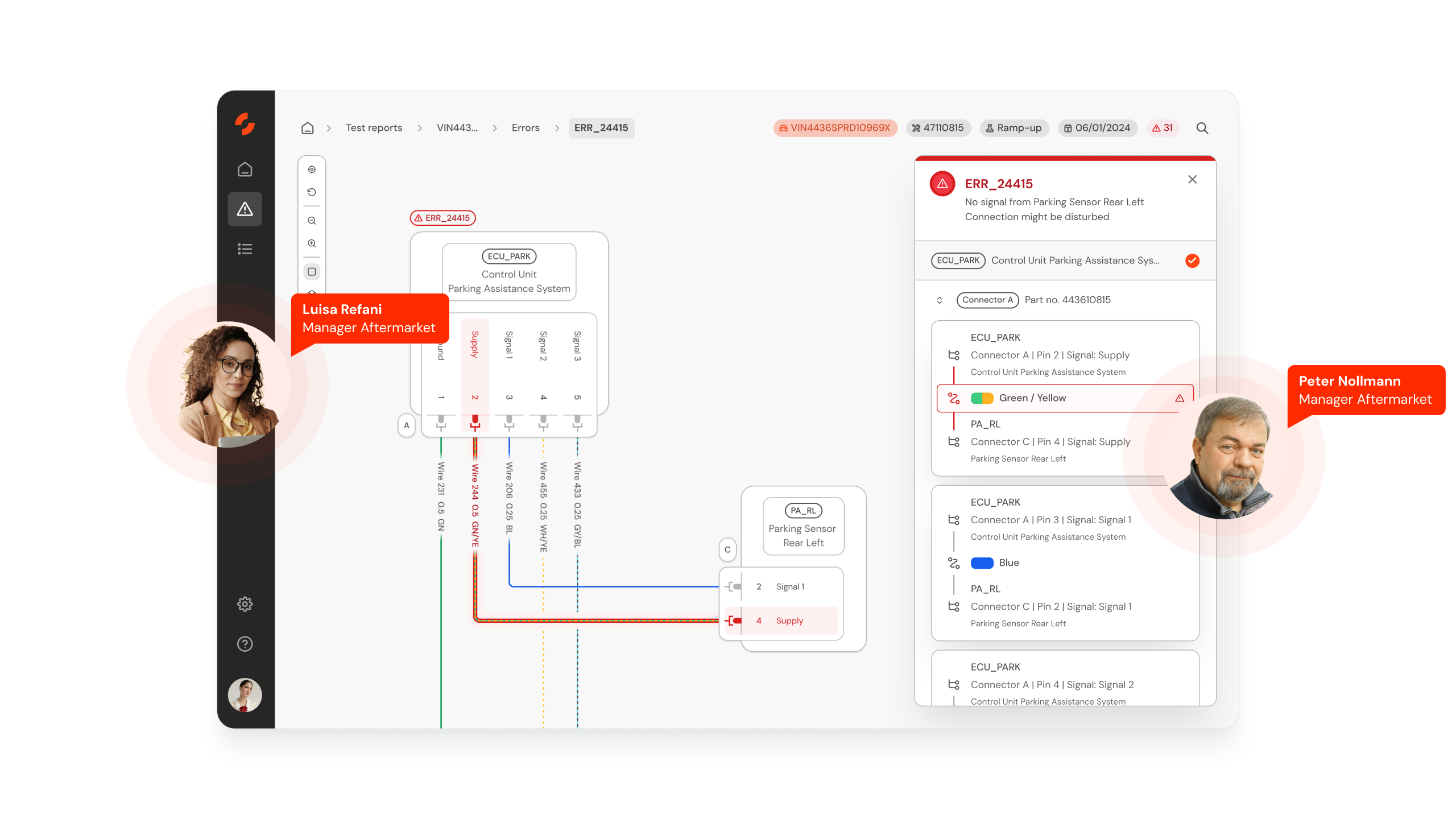
Step 1
See the matching 3D model
Get the correct CAD model of the vehicle in question in a web-based 3D view in which the service employee can quickly view the installed components.
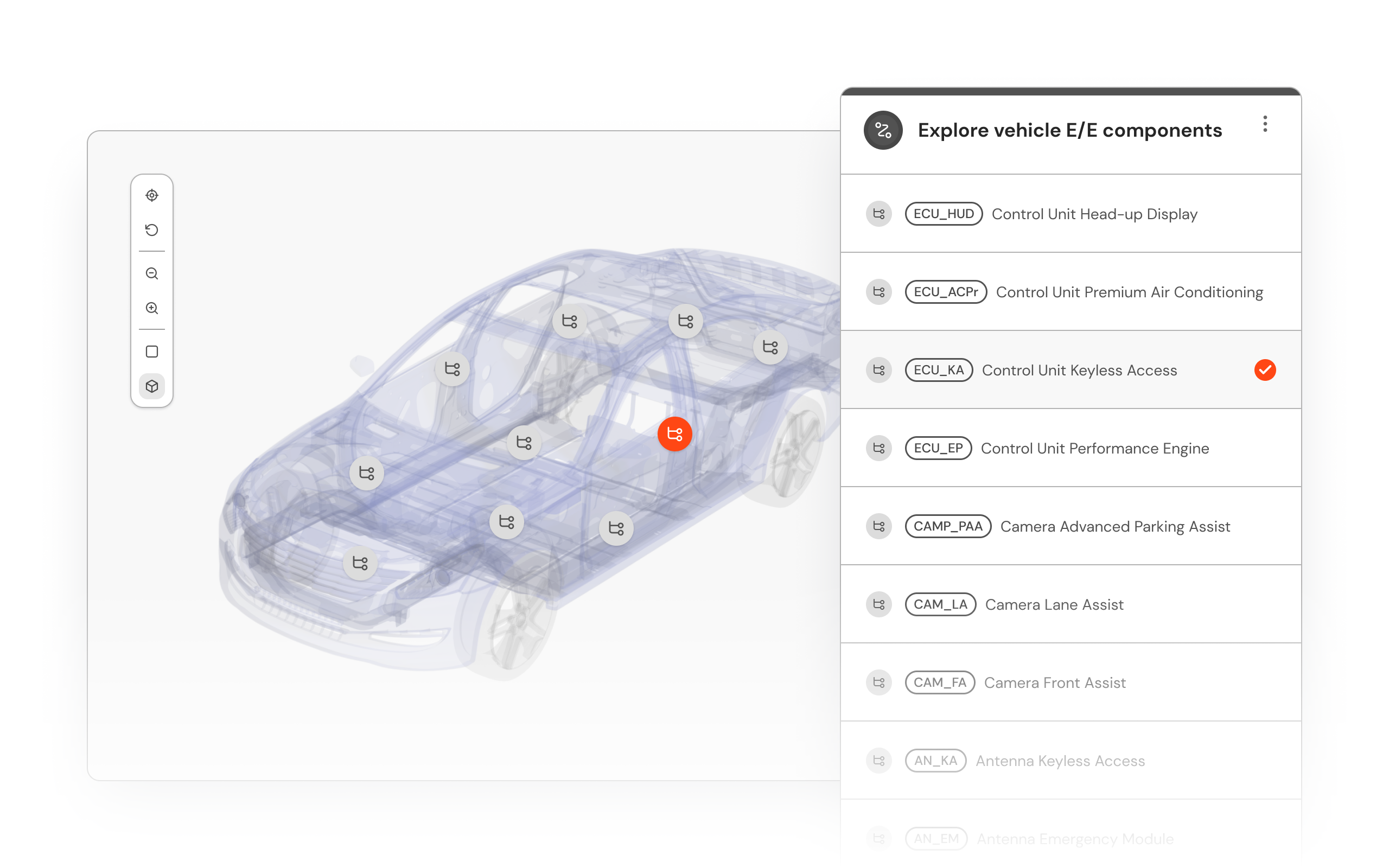
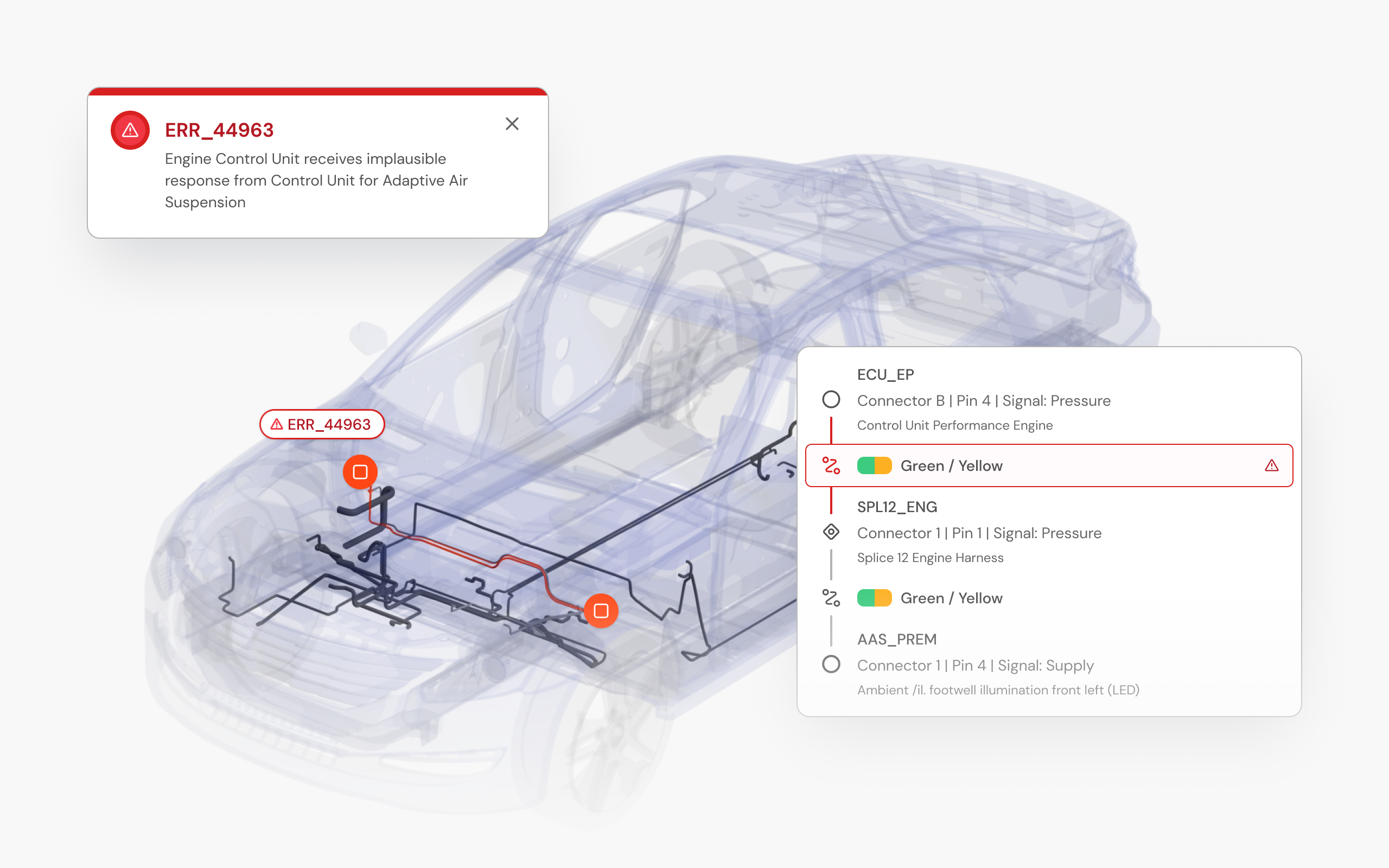
Step 2
Get E/E & SW error suggestions
From the DTCs or other error codes, our data model determines possible causes of errors based on the architecture logic and the product data and highlights them in the 3D model. This enables the service team to find the right troubleshooting solution more quickly.
Step 3
Find and fix faulty components
The affected components can be further explored via the 2D circuit diagram, allowing faulty control units, fuses, grounds, switches or other electrical components to be quickly located and fixed.
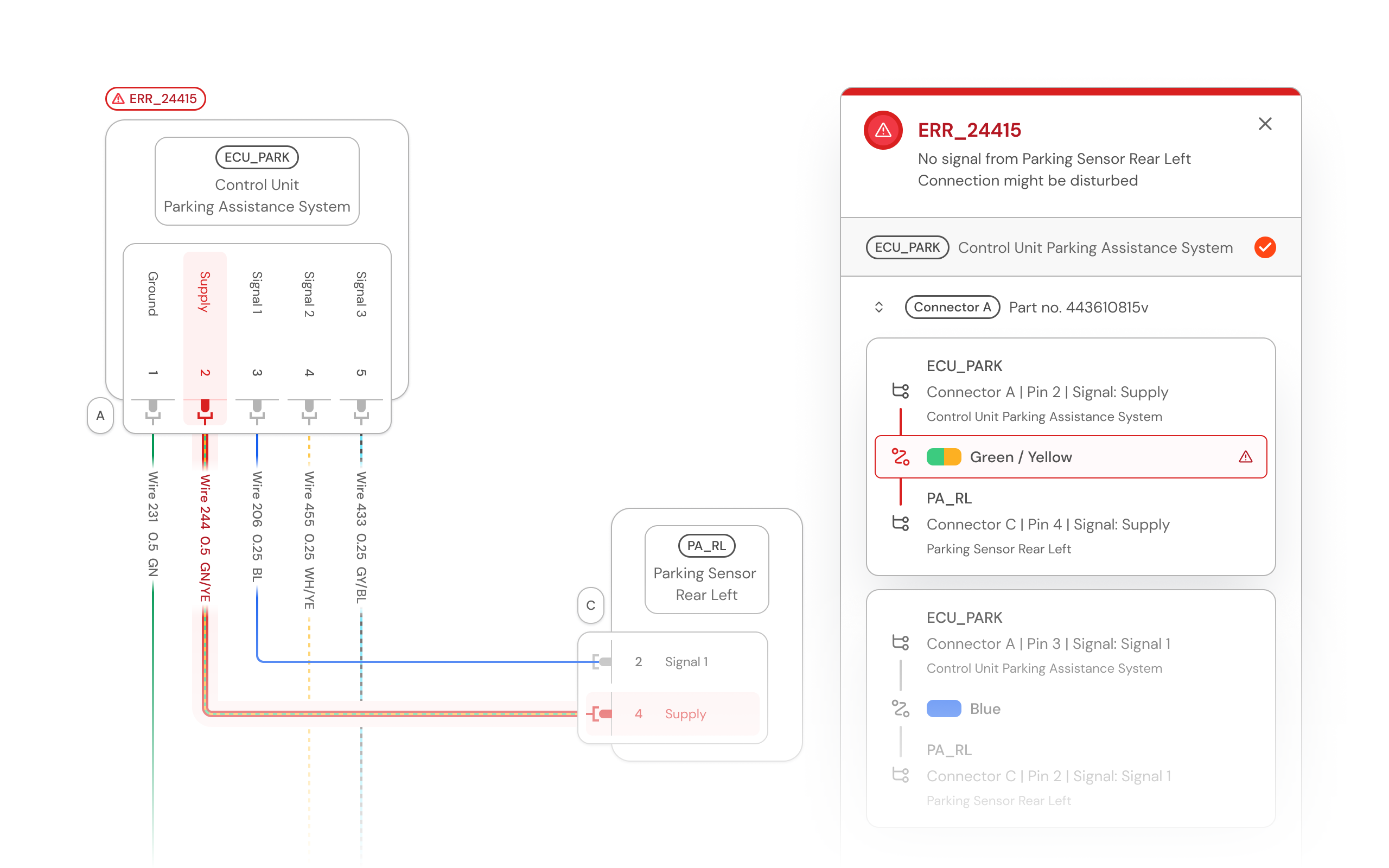
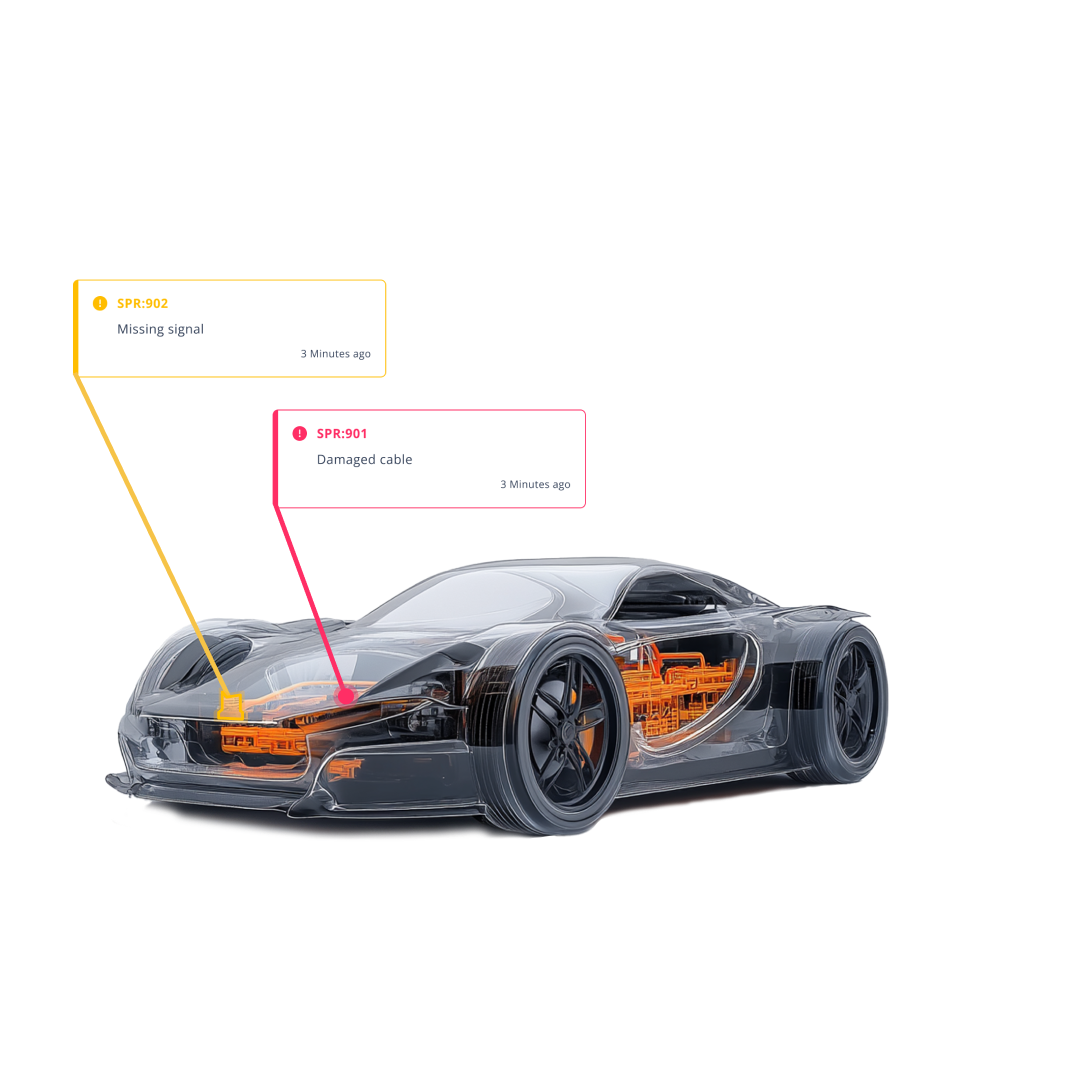
Find and solve E/E & software issues earlier across the lifecycle
With our error diagnostic application, engineers and service technicians reduce the time needed for troubleshooting malfunctions in mechatronic systems during R&D, Production, and Aftermarket.
Learn MoreExplore what you can do with SPREAD
Get a tour of our product and its use cases from one of our experts.
With SPREAD, you can:
- Create your organization's own knowledge graph to get end-to-end transparency of your product information
- Visualize relationships between a product's different domains and elements and increase your team's delivery speed
- Use preconfigured applications or build custom ones that give you the control and flexibility you need over the product information required for your specific use case
Simply fill out the form and we'll reach out shortly!